В центробежных циклонных аппаратах
Содержание
Ведение…………………………………………………… 1. Очистка газов от пыли в центробежных циклонных аппаратах………………………………………………… 1.1. Достоинства циклонных аппаратов и их классификация . 1.2. Условия работы циклонов …………………………….. 1.3. Эффективность улавливания ………………………….. 1.4. Пример расчета и подбора стандартного батарейного циклона …………………………………………………. 1.4.1. Исходные данные для расчета ……………………… 1.4.2. Расчет батарейного циклона ………………………… 2. Очистка газов в рукавных фильтрах………………... 2.1. Основные механизмы улавливания твердых частиц при фильтрации газа …………………………………… 2.1.1. Броуновская диффузия ……………………………… 2.1.2. Эффект касания или зацепления ……………………. 2.1.3. Инерционное осаждение …………………………… 2.2. Классификация тканевых рукавных фильтров и выбор фильтровальных тканей ………………………… 2.3. Аэродинамическое сопротивление тканевых фильтров ... 2.4. Пример расчета стандартного рукавного фильтра … 2.4.1. Исходные данные для расчета ……………………… 2.4.2. Расчет рукавного фильтра …………………………... 3. Очистка газов в электрофильтре…………………….. 3.1. Принцип действия электрофильтров …………………. 3.2. Классификация электрофильтров …………………….. 3.3. Эффективность очистки газа в электрофильтре ……... 3.4. Пример расчета электрофильтра ……………………… 3.4.1. Исходные данные для расчета ……………………… 3.4.2. Расчет электрофильтра ……………………………… 4. Библиографический список…………………………... |
Основные обозначения
C – концентрация пыли в газовом потоке, г/м3;
D – коэффициент диффузии, м2/с;
dm – средний размер частиц данной фракции, мкм;
dвол – диаметр волокна фильтровальной ткани, мкм;
F – площадь поперечного сечения аппарата, м2;
Fф – площадь фильтрующей поверхности, м2;
Gг – количество пыли в газовом потоке, г/сек;
n – количество фракций пыли;
P – давление газа , Па;
ΔР – гидравлическое сопротивление аппарата, Па;
T – температура газа, К;
Vг – объем отходящих газов, м3/ч;
Wг – скорость газового потока, м/с;
ηф – фракционная эффективность очистки газового потока от пыли;
Ση – общая эффективность очистки газа от пыли в аппарате;
ρ – плотность, кг/м3;
t – время пребывания газа в аппарате, с;
μг – динамическая вязкость газа, Па∙с;
Фi – доля i-й фракции пыли (i=1,n).
Введение
В XXI веке человечество подошло к такой «черте», когда почти каждый житель планеты понимает необходимость охраны окружающей среды, где особое место занимает защита атмосферного воздуха от загрязнений, которые выбрасываются на промышленных предприятиях из стационарных источников (выхлопных труб, вентиляционных коробов, факелов и градирен). Загрязнение атмосферы осуществляется твердыми, жидкими и газообразными отходами. В данном учебном пособии рассматриваются выбросы с отходящими газами твердых веществ или пыли. Выбросы могут осуществляться непрерывно, периодически при сжигании отходов или залпом при авариях. Наибольшее количество пыли попадает в атмосферу через выхлопные трубы, перед которыми необходимо устанавливать очистные сооружения. Степень очистки отходящих газов должна соответствовать ПДВ (предельно допустимый выброс), установленному экологическими службами данного региона для конкретного предприятия.
Отходящие газы могут быть холодными, когда их температура близка к температуре окружающей среды, – это вентиляционные газы из промышленных цехов, или нагретыми – это отходящие газы печей или сушильных аппаратов. Холодные газы плохо рассеиваются в атмосфере, поэтому обычно их рекомендуют подогревать.
Твердые частицы, находящиеся в отходящих газах, условно подразделяются на:
– пыль dm = 5 – 1000 мкм,
– дым dm = 0,1 – 5 мкм,
– аэрозоли dm = 0,001 – 0,1 мкм.
Такое условное деление позволяет классифицировать методы и оборудование для улавливания твердых частиц. Улавливание частиц 20–1000 мкм – грубая очистка газа от пыли, улавливание частиц менее 20 мкм до 1 мкм и менее – тонкая очистка газа, для улавливания аэрозольных частиц существуют особые методы очистки.
Сухая грубая очистка газа от пыли проводится механическими методами, где улавливание частицы ведется за счет воздействия на нее гравитационных, инерционных и центробежных сил.
Сухая тонкая очистка газа осуществляется за счет фильтрации газа через пористые перегородки. Тонкая очистка позволяет очищать газ и от аэрозольных частиц, если фильтрация газа идет в фильтрах, выполненных из ультратонких волокон.
Однако наиболее эффективно газ чистится от аэрозольных частиц в электрическом поле – это электрофильтры.
Степень очистки регламентируется предельно допустимыми концентрациями конкретного вещества в атмосфере (ПДК). Для недифференцированной пыли ПДК = 0,15 мг/м3, для пыли определенных веществ ПДК указаны в справочной литературе [9].
Для правильного проектирования аппаратов сухой очистки газов необходимо четко знать свойства твердых частиц, которые улавливаются. В первую очередь дисперсный состав, который обычно представляется в виде интегральных кривых. Большинство промышленных пылей подчиняются нормально логарифмическому закону распределения частиц по размеру. Следует отметить, что это характерно только для пылегазового потока, поступающего на первую ступень очистки газа, и не может быть использовано для расчета последующих аппаратов.
Важным параметром является плотность твердых частиц, чем она выше, тем эффективнее процесс улавливания. Необходимо учитывать адгезионные свойства частиц, т.е. склонность их к слипанию, что может привести к забиванию аппарата, абразивность частиц, их смачиваемость и гигроскопичность. Для электрофильтров важным параметром является удельное электрическое сопротивление слоя пыли, заряженность частиц и способность частиц пыли к самовозгоранию и образованию взрывоопасных смесей с воздухом.
В учебном пособии рассмотрены материалы по проектированию и подбору стандартного оборудования трех наиболее широко применяемых в промышленности очистки газовых выбросов аппаратов. Для грубой очистки газа от пыли используют одиночные или батарейные циклоны [3–8]. Для тонкой очистки газа – рукавные тканевые фильтры [3–8]. Для наиболее тонкой очистки газа с возможностью улавливания аэрозольных частиц рекомендованы электрофильтры [1–3, 10].
Очистка газов от пыли
в центробежных циклонных аппаратах
1.1. Достоинства циклонных аппаратов и их
классификация
Циклонные аппараты благодаря простоте устройства и обслуживания, сравнительно небольшому сопротивлению и высокой производительности являются наиболее распространенным типом сухого механического пылеуловителя. Циклонные пылеуловители имеют следующие преимущества:
– отсутствие движущихся частей в аппарате;
– надежность функционирования при температурах газов до 500 °С;
– возможность улавливания абразивных материалов при защите внутренних поверхностей циклонов специальными покрытиями;
– улавливание пыли в сухом виде;
– гидравлическое сопротивление аппаратов почти постоянно;
– аппараты успешно работают при высоких давлениях газов и при разряжении в аппарате;
– пылеуловители весьма просты в изготовлении;
– сохранение высокой фракционной эффективности очистки при увеличении запыленности газов.
По способу подвода газов в аппарат их подразделяют на циклоны со спиральным, тангенциальным, винтообразным и осевым подводом.
Наиболее предпочтительным по аэродинамике является подвод газов по спирали, однако, на практике все способы подвода могут применяться с равной эффективностью.
По конструкции корпуса циклоны подразделяют на цилиндрические и конические аппараты, последние предпочтительнее, так как скорость газа по мере движения возрастает и эффективность очистки увеличивается.
Циклоны могут устанавливаться в технологическом цикле, например, после печей обжига или при очистке хвостовых газов перед выбросом их в выхлопные трубы.
Условия работы циклонов
Газы, направляющиеся в аппарат, поступают в цилиндрическую часть циклона и совершают движение по спирали от периферии к центру, спускаются по наружной спирали, затем поднимаются по внутренней спирали. Частицы пыли отбрасываются центробежной силой к стенке циклона, а очищенные газы выходят через выхлопную трубу. Обычно в циклонах центробежное ускорение в тысячу раз больше ускорения силы тяжести. Поэтому даже весьма маленькие частицы пыли не в состоянии следовать за газом и под влиянием центробежной силы движутся к стенке аппарата.
Эффективность улавливания частиц пыли в циклоне характеризуется фактором разделения
, (1)
где w – окружная скорость движения частиц, м/с;
– радиус вращения, м;
g – ускорение свободного падения, м/с2.
Процесс целесообразно вести при увеличенных скоростях газа и меньших радиусах вращения частиц, т.е. при небольших диаметрах циклона . Однако увеличение скорости газа может привести и к резкому увеличению гидравлического сопротивления, что для процессов очистки отходящих газов неприемлемо. При очистке хвостовых газов газ откачивается из циклона вентилятором и должно соблюдаться отношение
, (2)
где – гидравлическое сопротивление циклона, Па;
rг – плотность газового потока в реальных условиях, кг/м3.
Увеличивать эффективность работы циклона целесообразно за счет уменьшения диаметра аппарата, что и привело к созданию батарейных циклонов. В промышленности принято разделять циклоны на высокопроизводительные и высокоэффективные. Высокоэффективные циклоны требуют больших затрат на осуществление процесса очистки. Высокопроизводительные циклоны имеют небольшое гидравлическое сопротивление, но хуже улавливают мелкие частицы, так как работают при меньших скоростях газа..
Диаметр одиночных цилиндрических циклонов обычно не превышает 2000 мм, а конических – 3000 мм. Для батарейных циклонов диаметры изменяются от 400 – 1200 мм, а количество циклонов в батарее от 2 до 8.
Эффективность улавливания
Эффективность очистки газа выражается отношением количества уловленной пыли к количеству пыли, поступившей в газоочистительный аппарат с газовым потоком за определенный период времени
, (3)
где – массовый расход частиц пыли, содержащейся в газовом потоке, в поступающем и выходящем потоках из аппарата соответственно, г/с;
– объемный расход газового потока поступающего и выходящего из аппарата соответственно, м3/с;
– концентрация твердых частиц в газовом потоке, поступающем в аппарат и выходящем из него соответственно, г/м3.
Эффективность очистки для частиц пыли различных размеров неодинакова. Лучше улавливается крупная пыль, поэтому первоначально степень очистки газов определяют по фракциям.
Зная фракционную степень очистки газов, можно определить общую эффективность очистки в аппарате:
, (4)
где Ф1, Ф2, Фn – доля определенной фракции пыли в газовом потоке, %;
n – количество фракций.
Суммарную степень очистки газов , достигаемую в нескольких последовательно установленных аппаратах (k), рассчитывают по формуле:
(5)
,
где – степень очистки газов от пыли в первом, втором и k аппарате соответственно.
Коэффициент проскока частиц пыли (степень неполноты улавливания пыли), в долях можно определить
. (6)
Для расчета фракционной эффективности улавливания необходимо четко знать фракционный состав пыли, т.е. дисперсность частиц в газовом потоке. Данные по дисперсному составу пыли в газовом потоке получают с помощью каскадных импакторов, принцип действия которых основан на инерционной сепарации частиц по размерам при пропускании пробы газа через ряд последовательно установленных сопл и подложек (рис.1). Размеры сопла уменьшаются по высоте аппарата. Определяют вес частиц в каждой подложке и относительную долю этих частиц в общем потоке.
Приведем пример замера фракционного состава пыли в газовом потоке. По результатам замера строим гистограмму (рис. 2.) и заносим значения в табл. 1.
Рис.1. Каскадный импактор:
1 − корпус, 2 – подложка, 3 – сопло, 4 – фильтр
|
|
Таблица 1
Диапазон по размеру частиц, dч, мкм | Средний размер частицы, dm, мкм | Фракционный состав, Ф, % | Дифференциальная составляющая, N, % | Интегральная составляющая, R, % |
1−5 | 2,5 | 2,5 | (100−7) = 93 | |
5−10 | 7,5 | 4,0 | (100−14) −10 = 76 | |
10−20 | 3,0 | (100−14−20) −15 = 51 | ||
20-−30 | 1,5 | (100−14−20−30) − −7,5 = 28,5 | ||
30−40 | 1,1 | (100−14−20−30−15) − −5,5 = 15,5 | ||
40−50 | 1,0 | (100−14−20−30−15−11) −5 = 5 |
Если процентное содержание каждой фракции разделить на разность размеров частиц, принятых в качестве граничных, и построить график N = f(dm), то получим дифференциальную кривую распределения частиц по размерам (рис.3).
При переходе к интегральным кривым R = f(dm), принимаем, что каждая точка кривой показывает относительное содержание частиц с размерами больше данного размера.
На рис. 4. представлено интегральное распределение частиц в линейной системе координат.
|
|
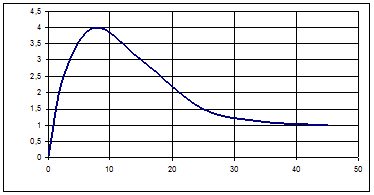
Рис.3. Дифференциальная кривая распределения частиц по размерам
|
|
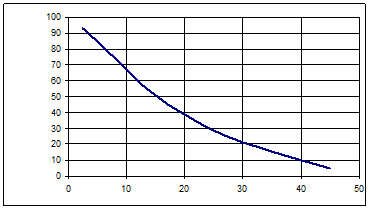
Рис. 4. Интегральная кривая распределения частиц по размерам
При построении функции R = f(dm) в вероятностно-логарифмических координатах (рис. 5) получаем прямую линию.
|
|
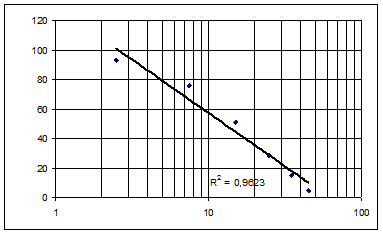
Рис.5. Интегральное распределение R = f(dm), в вероятностно-логарифмической системе координат
Если построить в логарифмических координатах зависимость эффективности улавливания от размера частиц, то получим зависимость ηФ= f(dm), которая может быть записана в виде интеграла вероятности
, (7)
где d50 − диаметр частицы, осаждаемый в циклоне при заданном гидродинамическом режиме работы на 50 % (экспериментальная величина);
lgsh − стандартное отклонение функции распределения фракционных коэффициентов.
Для расчета фракционной эффективности уравнение (7) можно упростить, выделив величины t и x:
, (8)
где , (9)
, (10)
В соответствии с известным дисперсным составом пыли графически можно решить интеграл (8), используя значение функции нормального распределения приведенных в литературе [8] и в табл. 2.
. (11)
Следует иметь в виду, что при расчете эффективности улавливания форма частиц не учитывается, хотя известно, что частицы, например, в форме чешуек, волокон или пластин улавливаются хуже, чем шарообразные. Однако все частицы в расчете принимаются шарообразной формы и определенный размер частицы характеризуется скоростью ее осаждения и плотностью (размер частиц по Стоксу).
Далее приведена таблица плотности твердых материалов улавливаемой пыли (табл. 3).
Значение плотности материала (пыли) необходимы при пересчете экспериментального значения d50 на новую расчетную величину, соответствующую данной системе пылеулавливания.
Например, для циклонов марки ЦН-15 экспериментально определены d50* = 4,5 мкм и lg*sη = 0,352. Эксперимент проводился для циклонов = 600мм при средней скорости газа в аппарате Wг* = 3,5 м/с, вязкости газа mг* = 22,2×10-6 Па×с и плотности частиц пыли rч* = 1930 кг/м3.
Таблица 2
Значение функции нормального распределения
![]() | ![]() | ![]() | ![]() | ![]() | ![]() | ![]() | ![]() | |
-2,70 | 0,0035 | -1,06 | 0,1446 | 0,00 | 0,5000 | 1,08 | 0,8599 | |
-2,60 | 0,0047 | -1,04 | 0,1492 | 0,02 | 0,5080 | 1,10 | 0,8643 | |
-2,50 | 0,0062 | -1,02 | 0,1539 | 0,04 | 0,5160 | 1,12 | 0,8686 | |
-2,40 | 0,0082 | -1 00 | 0,1587 | 0,06 | 0,5239 | 1,14 | 0,8729 | |
-2,30 | 0,0107 | -0,98 | 0.1635 | 0,08 | 0,5319 | 1,16 | 0,8770 | |
-2,20 | 0,0139 | -0,96 | 0,1685 | 0,10 | 0,5398 | 1,18 | 0,8810 | |
-2,10 | 0,0179 | -0,94 | 0,1736 | 0,12 | 0,5478 | 1,20 | 0,8849 | |
-2,00 | 0,0228 | -0,92 | 0,1788 | 0,14 | 0,5557 | 1,22 | 0,8888 | |
-1,98 | 0,0239 | -0,90 | 0,1841 | 0,16 | 0,5636 | 1,24 | 0,8925 | |
-1,96 | 0,0250 | -0,88 | 0,1894 | 0,18 | 0,5714 | 1,26 | 0,8962 | |
-1,94 | 0,0262 | -0,86 | 0,1949 | 0,20 | 0,5793 | 1,28 | 0,8997 | |
-1,92 | 0,0274 | -0,84 | 0,2005 | 0,22 | 0,5871 | 1,30 | 0,9032 | |
-1,90 | 0,0288 | -0,82 | 0,2061 | 0,24 | 0,5948 | 1,32 | 0,9066 | |
-1,88 | 0,0301 | - 0,80 | 0,2119 | 0,26 | 0,6026 | 1,34 | 0,9099 | |
-1,86 | 0,0314 | -0,78 | 0,2177 | 0,28 | 0,6103 | 1,36 | 0,9131 | |
-1,84 | 0,0329 | -0,76 | 0,2236 | 0,30 | 0,6179 | 1,38 | 0,9162 | |
-1,82 | 0,0344 | -0,74 | 0,2297 | 0,32 | 0,6255 | 1,40 | 0,9192 | |
-1,80 | 0,0359 | -0,72 | 0,2358 | 0,34 | 0,6331 | 1,42 | 0,9222 | |
-1,78 | 0,0375 | -0,70 | 0,2420 | 0,36 | 0,6406 | 1,44 | 0,9251 | |
-1,76 | 0,0392 | -0,68 | 0,2483 | 0,38 | 0,6480 | 1,46 | 0,9279 | |
-1,74 | 0,0409 | -0,66 | 0,2546 | 0,40 | 0,6554 | 1,48 | 0.9306 | |
-1,72 | 0,0427 | -0,64 | 0,2611 | 0,42 | 0,6628 | 1,50 | 0,9332 | |
-1,70 | 0,0446 | -0,62 | 0,2676 | 0,44 | 0,6700 | 1,52 | 0,9357 | |
-1,68 | 0,0465 | -0,60 | 0,2743 | 0,46 | 0,6772 | 1,54 | 0,9382 | |
-1,66 | 0,0485 | -0,58 | 0,2810 | 0,48 | 0,6844 | 1,56 | 0,9406 | |
-1,64 | 0,0505 | -0,56 | 0,2877 | 0,50 | 0,6915 | 1,58 | 0,9429 | |
-1,62 | 0,0526 | -0,54 | 0,2946 | 0,52 | 0,6985 | 1,60 | 0,9452 | |
-1,60 | 0,0548 | -0,52 | 0,3015 | 0,54 | 0,7054 | 1,62 | 0,9474 | |
-1,58 | 0,0571 | -0,50 | 0,3085 | 0,56 | 0,7123 | 1,64 | 0,9495 | |
-1,56 | 0,0594 | -0,48 | 0,3156 | 0,58 | 0,7190 | 1,66 | 0,9515 | |
-1,54 | 0,0618 | -0,46 | 0,3228 | 0,60 | 0,7257 | 1,68 | 0,9535 | |
-1,52 | 0,0643 | -0,44 | 0,3300 | 0,62 | 0,7324 | 1,70 | 0,9554 | |
-1,50 | 0,0668 | -0,42 | 0,3372 | 0,64 | 0,7389 | 1,72 | 0,9573 | |
-1,48 | 0,0694 | -0,40 | 0,3446 | 0,66 | 0,7454 | 1,74 | 0,9591 | |
Продолжение табл. 2 | ||||||||
| ||||||||
-1,46 | 0,0721 | -0,38 | 0,3520 | 0,68 | 0,7517 | 1,76 | 0,9608 | |
-1,44 | 0,0749 | -0,36 | 0,3594 | 0,70 | 0,7580 | 1,78 | 0,9625 | |
-1,42 | 0,0778 | -0,34 | 0,3669 | 0,72 | 0,7642 | 1,80 | 0,9641 | |
-1,40 | 0,0808 | -0,32 | 0,3745 | 0,74 | 0,7703 | 1,82 | 0,9656 | |
-1,38 | 0,0838 | -0,30 | 0,3821 | 0,76 | 0,7764 | 1,84 | 0,9671 | |
-1,36 | 0,0869 | -0,28 | 0,3897 | 0,78 | 0,7823 | 1,86 | 0,9686 | |
-1,34 | 0,0901 | -0,26 | 0,3974 | 0,80 | 0,7881 | 1,88 | 0,9699 | |
-1,32 | 0,0934 | -0,24 | 0,4052 | 0,82 | 0,7939 | 1,90 | 0,9713 | |
-1,30 | 0,0968 | -0,22 | 0,4129 | 0,84 | 0,7995 | 1,92 | 0,9726 | |
-1,28 | 0,1003 | -0,20 | 0,4207 | 0,86 | 0,8051 | 1,94 | 0,9738 | |
-1,26 | 0,1038 | -0,18 | 0,4286 | 0,88 | 0,8106 | 1,96 | 0,9750 | |
-1,24 | 0,1075 | -0,16 | 0,4364 | 0,90 | 0,8159 | 1,98 | 0,9761 | |
-1,22 | 0,1112 | -0,14 | 0,4443 | 0,92 | 0,8212 | 2,00 | 0,9772 | |
-1,20 | 0,1151 | -0,12 | 0,4522 | 0,94 | 0,8264 | 2,10 | 0,9821 | |
-1,18 | 0,1190 | -0,10 | 0,4602 | 0,96 | 0,8315 | 2,20 | 0,9861 | |
-1,16 | 0,1230 | -0,08 | 0,4681 | 0,98 | 0,8365 | 2,30 | 0,9893 | |
-1,14 | 0,1271 | -0,06 | 0,4761 | 1,00 | 0,8413 | 2,40 | 0,9918 | |
-1,12 | 0,1314 | -0,04 | 0,4840 | 1,02 | 0,8461 | 2,50 | 0,9938 | |
-1,10 | 0,1357 | -0,02 | 0,4920 | 1,04 | 0,8508 | 2,60 | 0,9953 | |
- 1,08 | 0,1401 | -0,00 | 0,5000 | 1,06 | 0,8554 | 2,70 | 0,9965 |
Таблица 3
Материал пыли | Плотность, ρч кг/м3 | Материал пыли | Плотность, ρч кг/м3 | |
Апатит | Сода кристаллическая | |||
Винипласт | Соль каменная | |||
Гипс кристаллический | Селитра натриевая | |||
Глина сухая | Сосна | |||
Зола | Текстолит | |||
Известняк | Уголь древесный | |||
Кокс | Уголь каменный | |||
Колчедан | Фаолит | |||
Песок сухой | Фосфорит | |||
Поташ | Цемент |
Для новой системы d50 можно определить по эмпирическому уравнению
. (12)
Пример расчета и подбора