Геометрические параметры и измерения
УГЛОВ РЕЖУЩЕЙ ЧАСТИ РЕЗЦОВ
ЦЕЛЬ РАБОТЫ
Практическое знакомство с конструкцией резцов и геометрическими параметрами их элементов, средствами и техникой измерения отдельных конструктивных элементов и геометрических параметров резцов.
ПРИМЕНЯЕМОЕ ОБОРУДОВАНИЕ
Универсальный угломер;
масштабная линейка;
штангенциркуль.
ТЕОРЕТИЧЕСКОЕ ВВЕДЕНИЕ
Обработка материалов резанием является одним из основных способов формообразования деталей.
Существуют различные методы обработки материалов резанием: точение, сверление, строгание, фрезерование, протягивание и т. д. Для каждого метода создан свой инструмент, обладающий только ему присущими характеристиками. Однако все они имеют одно общее – резание осуществляется режущим клином. Наиболее наглядно режущий клин представлен у резцов. Поэтому изучение основных геометрических параметров клина целесообразно провести на примере этого инструмента [1, 2].
При измерении углов токарного резца принимаются две координатные плоскости – основная плоскость и плоскость резания (рисунок 1).
Рисунок 1 – Координатные плоскости.
Кроме этого рассматриваются еще две плоскости – главная и вспомогательная секущие плоскости.
Главной секущей плоскостью называется плоскость, перпендикулярная к проекции главной режущей кромки на основную плоскость.
Вспомогательной секущей плоскостью называется плоскость перпендикулярная к проекции вспомогательной режущей кромки на основную плоскость.
У токарного резца различают главные и вспомогательные углы, которые измеряются соответственно в главной и вспомогательной секущих плоскостях. Кроме того, резец имеет углы в плане и угол наклона главной режущей кромки (углы принято обозначать буквами греческого алфавита).
Таким образом, в резце различают:
– главный задний угол, образован главной задней поверхностью резца и плоскостью резания;
– вспомогательный задний угол, образован вспомогательной задней поверхностью резца и плоскостью, проходящей через вспомогательную режущую кромку и перпендикулярной основной плоскости;
– передний угол, образован передней поверхностью резца и плоскостью перпендикулярной к плоскости резания;
– угол резания, образован передней поверхностью резца и плоскостью резания;
– угол заострения, образован передней и главной задней поверхностями резца;
– главный угол в плане, образован проекцией главной режущей кромки на основную плоскость и направлением подачи;
– вспомогательный угол в плане, образован проекцией вспомогательной режущей кромки на основную плоскость и направлением подачи;
– угол при вершине резца, образован проекциями главной и вспомогательной режущих кромок на основную плоскость, проходящей через вершину резца;
– угол наклона главной режущей кромки, образован главной режущей кромкой и плоскостью, проходящей через вершину резца, параллельно основной плоскости.
На рисунке 2 приведены углы токарного резца, их обозначения, главная и вспомогательная
секущие плоскости. Измерением на универсальном настольном угломере определяются величины следующих углов:
,
,
,
,
,
. Остальные определяются по формуле (1):
![]() | (1) |
На рисунке 3 приведена схема устройства универсального настольного угломера и методы измерения углов. Универсальный угломер состоит из плиты 1, служащей одновременно основной плоскостью, вертикальной стойки 2, на которой перемещается головка, состоящая из блока трех шкал с поворотными угольниками и указателями.
Рисунок 2 – Углы токарного резца.
Для измерения переднего угла и задних углов
и
служит шкала 3 и угольник 4. Пластина шкалы 3 устанавливается перпендикулярно главной режущей кромке и перемещается до соприкосновения с передней поверхностью резца горизонтальной линейки угольника.
Значение переднего угла отсчитывается от нуля шкалы до штриха на измерительном угольнике (рисунок 3 а). Может быть два положения указателя – влево или вправо от нуля. В первом случае угол
будет положительным, во втором – отрицательный. Измерение заднего угла
производится аналогично измерению переднего. В этом случае линейка угольника доводится до полного контакта с главной задней поверхностью резца. Отсчет значения угла
производится вправо от нуля (рисунок 3 а).
Измерение вспомогательного заднего угла производится таким же образом. Шкала 3 устанавливается перпендикулярно вспомогательной режущей кромке, а линейка должна плотно прилегать к задней поверхности.
Для измерения главного и вспомогательного углов в плане и
используют горизонтальную шкалу 5 и линейку 6 с указателем. Головка поворачивается и закрепляется в требуемом положении. Измерительная головка на стойке закрепляется таким образом, чтобы наружная поверхность линейки 6 была расположена перпендикулярно направляющей планке 7, а указатель показывал нуль. Измеряемый резец кладут на плитку и боковой поверхностью прижимают к направляющей планке 7 (рисунок 3 б). Резец перемещают вдоль планки и поворачивая линейку влево до соприкосновения с главной режущей кромкой, производят отсчет угла
по шкале влево от нуля. Угол
измеряется подобным же образом, если линейку угольника повернуть вправо до соприкосновения с вспомогательной режущей кромкой (при этом отсчет угла будет производиться по шкале вправо от нуля).
При измерении угла наклона главной режущей кромки поворачивают измерительную головку со шкалой до тех пор, пока она не станет параллельна главной режущей кромке. Для этого необходимо повернуть линейку 9 и опустить измерительную головку так, чтобы линейка пришла в соприкосновение с главной режущей кромкой резца (рисунок 3 в). На шкале 8 можно произвести отсчет угла
. Если линейка и указатель будут повернуты вправо, то угол
будет положительным, если влево – отрицательным. Если указатель совпадает с нулевым делением, то угол
равен нулю.
|
|
|
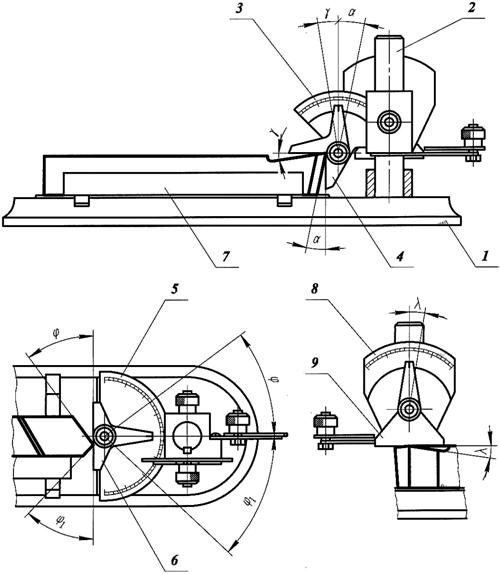
Рисунок 3 – Способы измерения углов резца универсальным угломером:
а) углы и
; б) углы
и
; в) угол
.
Геометрические размеры токарного резца измеряются штангенциркулем и линейкой. Все полученные значения геометрических и угловых параметров токарного резца заносятся в сводную таблицу 1.
Таблица 1 – Результаты измерения токарного резца.
№ п/п | Тип резца | Материал режущей части | Геометрические и угловые параметры токарного резца: | |||||||||||
Геометрические, ![]() | Угловые, ![]() | |||||||||||||
Сечение державки ![]() | Длина резца ![]() | Смещение вершины ![]() | ![]() | ![]() | ![]() | ![]() | ![]() | ![]() | ![]() | ![]() | ![]() | |||
ПОРЯДОК ВЫПОЛНЕНИЯ РАБОТЫ
4.1. Перед выполнением работы студенты должны ознакомиться с правилами по технике безопасности и с инструкцией по общим правилам работы в лаборатории;
4.2. Изучить методические указания и справочную литературу;
4.3. Измерить геометрические и угловые параметры токарного резца, согласно вышеописанной методике;
4.4. Сделать в необходимом количестве проекций рабочий эскиз рассматриваемого резца с простановкой на нем измеренных (и рассчитанных) геометрических и угловых параметров;
4.5. Сделать эскиз общего вида универсального угломера;
4.6. Составить отчет по выполненной работе.
ЛИТЕРАТУРА
[1] Вульф А.М. Основы резания металлов. – М.: Машгиз, 1973 – 240с.
[2] Грановский Г.И., Грановский В.Г. Резание металлов: Учебник для машиностр. и приборостр. спец. вузов. – М.: Высш. шк., 1985. – 304 с., ил.
Лабораторная работа №2
ИЗУЧЕНИЕ ДЕФОРМАЦИЙ ПРИ СТРУЖКООБРАЗОВАНИИ
(УСАДКА СТРУЖКИ)
ЦЕЛЬ РАБОТЫ
Экспериментальным путем определить влияние скорости резания, глубины резания, подачи, угла резания и обрабатываемого материала на усадку стружки при точении.
ПРИМЕНЯЕМОЕ ОБОРУДОВАНИЕ
Токарно-винторезный станок модели
;
поперечно-строгальный станок модели 7212;
токарные и строгальные резцы;
образцы-заготовки из разных материалов (сталь 45,
,
, алюминий, медь);
масштабная линейка;
торсионные весы;
гибкая нить.
ТЕОРЕТИЧЕСКОЕ ВВЕДЕНИЕ
Резание металлов представляет собой сложный процесс, состоящий из упругой и пластической деформации, а также разрушения. Срезаемый слой обрабатываемой детали удаляется из зоны резания в виде стружки. Размеры и форма стружки могут значительно отличаться от размеров и формы срезаемого слоя. Таким образом, изменение размеров стружки по сравнению с размерами срезаемого слоя может в определенной степени характеризовать пластическую деформацию срезаемого слоя при резании. Эту характеристику принято называть усадкой стружки.
Усадка стружки (обозначаемая буквой греческого алфавита ) определяется физико-механическими свойствами обрабатываемого материала, материалом и геометрией режущей части инструмента, режимами резания (скорость, подача и глубина резания).
В процессе резания срезаемый слой подвергается объемной деформации, в результате чего стружка уменьшается по длине и увеличивается по толщине и ширине. При этом объем срезаемого металла не меняется [1].
На рисунке 1 приведена схема стружкообразования и сопоставление размеров элемента срезаемого слоя металла. Считая, что объем срезаемого металла до и после деформации не меняется, то:
![]() | (1) |
где ,
,
– соответственно глубина, ширина и длина срезаемого слоя;
,
,
– соответственно глубина, ширина и длина стружки.
Из равенства (1) следует, что:
![]() | (2) |
Отношение называется продольной усадкой стружки, а отношение
– поперечной усадкой стружки.
Согласно справочника [1], численно можно считать .
Рисунок 1 – Упрощенная схема стружкообразования.
Существуют несколько методов по определению усадки стружки. Рассмотрим некоторые из них.
Метод №1 Определение усадки стружки по углу сдвига.
Этот метод заключается в том, что зная угол сдвига (определяется путем металлографического исследования корня стружки), усадку стружки можно определить по следующей формуле:
![]() | (3) |
Рисунок 2 – Схема определения усадки стружки по углу сдвига.
Метод №2 Определение усадки стружки весовым методом.
Данный метод заключается в следующем:
а). На токарном станке проводят серию опытов и после каждой обработки от снятой стружки отламывают небольшой кусочек диной (длина отлома зависит от сечения среза – чем больше сечение, тем меньше кусочек отлома);
б). С помощью гибкой нити и линейки измеряют длину отломанного кусочка ,
и на торсионных весах его взвешивают
,
;
в). По полученным данным вычисляют сечение стружки:
![]() | (4) |
где – удельный вес обрабатываемого материала,
.
г). По данным протокола испытаний определяют сечение среза:
![]() | (5) |
где и
– соответственно глубина резания и подача (из протокола ис-
пытаний).
д). По найденным значениям определяется поперечная усадка стружки:
![]() | (6) |
е). Полученные результаты заносятся в сводную таблицу 1 и на основании этих значений строят соответствующие зависимости (рисунок 3).
Метод №3 Определение продольной усадки путем
измерения длины пути резца и длины стружки.
Данный метод заключается в следующем:
а). На поперечно-строгальном станке проводят серию опытов с образцами-заготовками одинаковой длины из различных материалов;
б). После каждого опыта выбирают три-четыре образца стружек и с помощью гибкой нити и линейки измеряют длину каждой стружки (длина пути резца при этом равна длине образцов);
в). По полученным результатам определяют среднюю длину стружки и рассчитывают продольную усадку стружки для каждой марки материала.
г). Полученные результаты заносятся в сводную таблицу 2 и на основании этих значений строят зависимость продольной усадки стружки от разных марок обрабатываемого материала (рисунок 4).
Таблица 1 – Протокол испытаний.
№ п/п | Углы режущей части резца | Диаметр заготовки | Скорость резания | Подача | Глубина резания | Длина стружки | Вес стружки | Сечение стружки | Сечение среза | Усадка стружки | |||
![]() | ![]() | ![]() | ![]() | ![]() ![]() | ![]() ![]() | ![]() ![]() | ![]() ![]() | ![]() ![]() | ![]() ![]() | ![]() ![]() | ![]() ![]() | ![]() | |
|
|
|
| |||
| |||
|
|
|
Рисунок 3 – Зависимость влияния различных факторов,
возникающих в процессе точения на усадку стружки.
Таблица 2 – Протокол испытаний.
№ п/п | Углы режущей части резца | Материал заготовки | Скорость резания | Подача | Глубина резания | Длина пути резца (длина образца) | Длина стружки | Усадка стружки | |||
![]() | ![]() | ![]() | ![]() | ![]() ![]() | ![]() ![]() | ![]() ![]() | ![]() ![]() | ![]() ![]() | ![]() | ||
|
|
Рисунок 4 – Влияние различных материалов на продольную усадку стружки.
ПОРЯДОК ВЫПОЛНЕНИЯ РАБОТЫ
4.1. Перед выполнением работы студенты должны ознакомиться с правилами по технике безопасности и с инструкцией по общим правилам работы в лаборатории;
4.2. Изучить методические указания и справочную литературу;
4.3. Экспериментальным путем определить характер влияния режимов резания и угла резания на усадку стружки;
4.4. На основании полученных результатов построить графики соответствующих зависимостей;
4.5. Составить отчет по выполненной работе.
ЛИТЕРАТУРА
[1] Вульф А.М. Основы резания металлов. – М.: Машгиз, 1973 – 240с.
[2] Грановский Г.И., Грановский В.Г. Резание металлов: Учебник для машиностр. и приборостр. спец. вузов. – М.: Высш. шк., 1985. – 304 с., ил.
Лабораторная работа №3