Кинетика процесса кристаллизации. Критический зародыш
При кристаллизации одновременно идут два процесса: образование зародышей (центров) кристаллизации и их рост. Зародыш минимального размера, устойчивый и способный к росту, называется критическим зародышем RКР. Зародыш меньшего размера будет растворяться в жидкой фазе. Размер критического зародыша зависит от степени переохлаждения: чем больше ΔТ, тем меньше RКР.
По мере развития процесса кристаллизации зародыши растут свободно, правильной геометрической формы, при их соприкосновении форма нарушается. Металл приобретает поликристаллическую структуру, состоящую из кристаллов неправильной формы – зёрен (рис.6). Размеры зёрен зависят от соотношения скоростей зарождения и роста зародышей. При малых степенях переохлаждения диффузионные процессы роста зародышей преобладают, их число невелико, и формируется крупнозернистая структура. С увеличением ΔТ диффузия атомов резко снижается, преобладает процесс роста числа зародышей и образуется мелкое зерно.
Размер зерна сильно влияет на механические свойства: у металла с мелким зерном выше прочность, пластичность и, особенно, вязкость. Для получения мелкого зерна широко применяют модифицирование – введение в расплав добавок, которые препятствуют росту зерна или создают много центров кристаллизации в виде тугоплавких дисперсных частиц, карбидов, нитридов и др.
Рис. 6. Схема образования поликристаллической структуры.
1. Виды и назначение отжига до- и заэвтектоидных сталей. Получаемые структура и свойства.
Цель отжига – получение равновесной структуры. Это достигается путем медленного охлаждения детали вместе с печью (рис. 38). Структуры сталей после отжига соответствуют равновесной диаграмме состояния (Fe-Fe3C):
· доэвтектоидных - П+Ф,
· эвтектоидной – П,
· заэвтектоидных – П+ЦII.
Виды отжига:
Рекристаллизационный отжиг проводится для снятия наклёпа. Температура нагрева сталей 650…700°С (Рис.39).
Отжиг для снятия остаточных напряжений (в отливках, сварных соединениях и др.) проводится при температуре 550..650°С.
Диффузионный отжиг (гомогенизация) применяется для легированных сталей с целью устранения химической и структурной неоднородности, Тнагр= 1100..1200°С (Рис.39), выдержка 15..20 часов. После диффузионного отжига формируется крупнозернистая структура (П+Ф).
Полный отжиг проводится для доэвтектоидных сталей с целью получения мелкозернистой равновесной структуры с пониженной твёрдостью и высокой пластичностью и снятия внутренних напряжений. Полный отжиг проводится при температуре на 30..50°С выше линии АС3 (Рис.38), происходит полная фазовая перекристаллизация, структура – П+Ф, мелкозернистая. Полный отжиг заэвтектоидных сталей не применяется, так как приводит к образованию структуры П+ЦII с хрупкой цементитной сеткой.
Неполный отжиг доэвтектоидных сталей проводится при температуре на 10…30°С выше линии АС1 (Рис.39) с целью снизить твёрдость для улучшения обработки резанием. Происходит частичная перекристаллизация. Применяется вместо полного отжига, если не требуется измельчение зерна.
Для заэвтектоидных сталей назначается только неполный отжиг. Он проводится при температуре на 10…30°С выше линии АС1 (Рис.39) с цельюполучения зернистого перлита. Такой отжиг называется сфероидизирующим.
Изотермический отжиг применяется для легированных сталей и заключается в нагреве выше линии АС3, быстром охлаждении до 620…660°Сс последующей изотермической выдержкой в течение 3…6 часов до полного распада аустенита с образованием сорбита пластинчатого. Далее ведут охлаждение на воздухе.
Рис. 39. «Стальной угол» диаграммы состояния Fe-Fe3C с нанесенными температурами нагрева при различных видах отжига
Расшифровать состав сплава АЛ2. Указать способ изготовления деталей из данного сплава и описать способ его упрочнения
Задача: Применяют среднеуглеродистые стали (0,3…0,5%С), обладающие повышенной вязкостью: 5ХНМ. Термообработка: закалка в масле+высокий отпуск. Структура: троостосорбит, твердость 40…45 HRC, рабочая температура – 500…550°С.
Углеродистая У12. Термообработка: закалка + низкий отпуск. Структура: мартенсит отпуска и вторичный цементит (карбиды). Твердость после термообработки 62…63 HRC.
Термообработка: закалка + средний отпуск. Структура - троостит отпуска. Свойства: высокие пределы упругости, текучести и выносливости 65СГ
20Х2Н4ВА Термообработка: цементация+закалка+низкий отпуск. Структура на поверхности: МОТП+ЦII+АОСТ
Билет № 16
1. Испытания на растяжение. Кривая растяжения и механические характеристики: предел прочности, предел текучести для пластичных и малопластичных материалов. Относительное удлинение и относительное сужение. Единицы измерения данных характеристик.
. Характеристики механических свойств, определяемые при статическом растяжении
σ |
а) |
Испытания на растяжение проводят на специальных машинах и стандартных образцах с начальной длиной l0 и площадью поперечного сечения F0 (рис. 8 а). Растягивающая нагрузка Р нарастает плавно, образец постепенно удлиняется и разрушается. При этом записывают диаграмму растяжения в координатах “нагрузка – удлинение образца”, которая приводится к диаграмме условных напряжений в координатах “напряжение (σ) - относительное удлинение (δ)” (рис.7). Напряжение – нагрузка (сила), действующая на единицу площади (σ=P/F0, МПа).
б) |
а) |
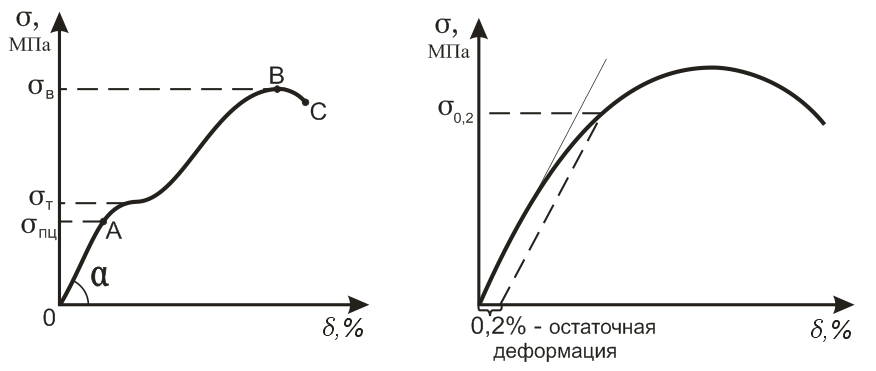
Рис.7. Диаграммы растяжения пластичного (а) и малопластичного (б) материалов
Тангенс угла наклона линейного участка диаграммы растяжения характеризует модуль упругости E=tgα.
Предел пропорциональности, σпц – максимальное напряжение, соответствующее линейному участку кривой растяжения.
Предел упругости, σупр – напряжение, при котором остаточная деформация принимает заданное значение 0,05% и меньше, обозначается – – σ0,002, σ0,02 и σ0,05.
Предел текучести, σТ – напряжение, при котором материал деформируется (течет) без увеличения нагрузки. Для пластичных материалов это напряжение соответствует площадке текучести (рис. 7 а). Для малопластичных материалов, применяют условный предел текучести, σ0,2– напряжение, вызывающее остаточную деформацию 0,2% (рис. 7б).
Предел прочности (временное сопротивление), σв – максимальное напряжение, предшествующее разрушению образца:
.
Относительное удлинение: δ = ∙100%; ιк – конечная длина образца.
Относительное сужение:ψ = ∙100%; Fк – площадь поперечного сечения в месте разрыва.
На диаграмму изотермического распада переохлажденного аустенита нанести режимы охлаждения при отжиге, нормализации и закалке. Назначение и виды этих процессов для до- и заэвтектоидных сталей. Получаемые структуры и свойства
Цель отжига – получение равновесной структуры. Это достигается путем медленного охлаждения детали вместе с печью (рис. 38). Структуры сталей после отжига соответствуют равновесной диаграмме состояния (Fe-Fe3C):
· доэвтектоидных - П+Ф,
· эвтектоидной – П,
· заэвтектоидных – П+ЦII.
Нормализация – это нагрев доэвтектоидных сталей на 40…50 °С выше АС3, заэвтектоидных – на 40..50°С выше АСm, выдержка и последующее охлаждение на спокойном воздухе (Рис.38, 40).
Рис. 40. «Стальной угол» диаграммы состояния Fe-Fe3C с нанесенными температурами нагрева при нормализации
При нагреве происходит полная фазовая перекристаллизация, в результате охлаждения получают высокодисперсные феррито-цементитные смеси. Структуры:
· доэвтектоидных сталей - С+Ф,
· эвтектоидной – С,
· заэвтектоидных – С+ЦII.
После нормализации сталь имеет более высокую прочность, твёрдость, сопротивление хрупкому разрушению, по сравнению с отжигом.
Цель нормализации - устранение крупнозернистой структуры, полученной при предшествующей обработке (литье, горячей прокатке, ковке или штамповке, диффузионном отжиге). Нормализацию применяют:
· для низкоуглеродистых сталей - вместо отжига,
· для среднеуглеродистых – вместо закалки с высоким отпуском,
· для высокоуглеродистых (заэвтектоидных) – для частичного устранения цементитной сетки,
· для некоторых легированных сталей – вместо закалки.
Азотирование. Назначение, режимы, применяемые стали и получаемые свойства
Азотирование – диффузионное насыщение поверхностного слоя стали азотом. Азотирование проводят при температуре 480…600°С в среде частично диссоциированого аммиака, который является источником атомарного азота: NH3→3/2H2+Nат. Длительность процесса азотирования составляет 24…60 часов для получения слоя толщиной 0,3…0,6 мм.
Азотированию подвергают среднеуглеродистые стали (0,3…0,5%С), легированные хромом, молибденом, алюминием, ванадием, например 38Х2МЮА (0,38%С, 2% Cr, 1% Al, 0,2% Mo). Азотированный слой имеет многофазное строение: на поверхности образуются нитриды железа (ε- и γ΄-фазы, Fe2-3N и Fe4N соответственно), а также нитриды легирующих элементов типа MeN и Me2N, которые придают высокую твёрдость (1100…1200 HV) азотированному слою.
Перед азотированием проводится термообработка, как правило, улучшение (закалка с высоким отпуском), с целью повышения прочности и вязкости сердцевины за счет формирования структуры сорбита зернистого. Затем проводят механическую обработку для придания окончательных размеров изделию, наносят защитные покрытия на участки, не подлежащие азотированию. После азотирования проводят окончательное шлифование изделия.
Азотирование повышает твердость, износостойкость, предел выносливости, сопротивление коррозии и применяется для упрочнения шестерен, гильз цилиндров, коленчатых и распределительных валов, клапанов двигателей внутреннего сгорания и т.д.
Задача: Применяют среднеуглеродистые стали (0,3…0,5%С), обладающие повышенной вязкостью: 5ХНМ. Термообработка: закалка в масле+высокий отпуск. Структура: троостосорбит, твердость 40…45 HRC, рабочая температура – 500…550°С.
Углеродистая У12. Термообработка: закалка + низкий отпуск. Структура: мартенсит отпуска и вторичный цементит (карбиды). Твердость после термообработки 62…63 HRC.
Термообработка: закалка + средний отпуск. Структура - троостит отпуска. Свойства: высокие пределы упругости, текучести и выносливости 65СГ
20Х2Н4ВА Термообработка: цементация+закалка+низкий отпуск. Структура на поверхности: МОТП+ЦII+АОСТ
Билет №17
1. Особенности превращения аустенита в перлит. Промежуточное превращение. Строение и свойства продуктов превращений.
Перлитное превращение
Перлитное превращение идет при переохлаждении аустенита в диапазоне температур 727˚С...500˚С. При этом происходит распад аустенита на феррито-цементитную смесь:
А0,8%С→Ф0,02%С+Ц6,67%С.
Механизм перлитного превращения – диффузионный и включает два процесса:
· диффузионное перераспределение углерода, приводящее к образованию цементита;
· полиморфное превращение Feγ→Feα (ГЦК→ОЦК) с образованием феррита.
В итоге образуется феррито-цементитная смесь пластинчатого строения. В зависимости от температуры переохлаждения образуются феррито-цементитные смеси, отличающиеся степенью дисперсности (межпластинчатым расстоянием Δ0): перлит, сорбит, троостит (табл. 2). С увеличением степени переохлаждения увеличивается дисперсность структур, повышается прочность и твёрдость. Наибольшей пластичностью и вязкостью обладает структура сорбита.
Таблица 2
Продукты перлитного превращения
Ф-Ц смесь | tпереохлаждения, °С | Структура | Межпластинчатое расстояние Δ0, мкм | Твердость, НВ |
Перлит | А1…650 | ![]() | 0,6…1,0 | 180…250 |
Сорбит | 650…550 | ![]() | 0,25…0,3 | 250…350 |
Троостит | 550…500 | ![]() | 0,1…0,15 | 350…450 |