Технология машинной формовки
Литниковые системы
Рис. 196. Элементы литниковой системы: 1- Литниковая чаша; 2 — стояк; 3— шлакоуловитель; 4 — питатели; 5, 6 -— чаша и стояк выпоров (прибылей); 7 — фильтр из специальной стеклоткани |
Литейную форму заливают расплавом через литниковую систему. Литниковой системой называют совокупность каналов и резервуаров, по которым расплав поступает из ковша в полость формы. Литниковая система должна обеспечить непрерывное поступление расплава в форму, питание отливки для компенсации усадки, предотвращать разрушение формы, попадание шлака и воздуха со струей расплава.
Основными элементами литниковой системы являются литниковая чаша, стояк, шлакоуловитель, питатели (рис. 196). Чаша уменьшает размывающее действие струи расплава, задерживает всплывающий шлак.
Для лучшего задержания шлака в литниковой системе для чугунного литья выдерживают следующее соотношение размера сечения стояка, шлакоуловителя и питателей: Fcт > Fшл >Fпит.
На верхних частях средних и крупных отливок делают в ы поры — каналы для выхода из формы воздуха и газов и всплывающих неметаллических включений. Они содействуют нормальной усадке застывающего сплава.
Литниковые системы в зависимости от формы, размера отливки, состава и свойств литейного сплава имеют различное, иногда сложное устройство (рис. 196).
г |
Верхняя литниковая система наиболее проста. Ее применяют для мелких деталей
небольшой высоты. С увеличением высоты происходит размывание формы струей расплава, разбрызгивание и окисление его, увеличивается количество неметаллических включении в теле отливки.
Нижнюю (или сифонную) литниковую систему применяют для средних и толстостенных отливок значительной высоты. Она обеспечивает спокойное заполнение формы расплавом. Вместе с тем эта система более сложна.
Ярусная литниковая система обеспечивает последовательное питание отливки снизу вверх, и ее применяют для крупных отливок. Недостатки ярусной литниковой системы — сложность в изготовлении и значительный расход расплава. Ее разновидность — вертикально-щелевая система — предназначается главным образом для цветных сплавов.
Для лучшего задержания шлаковых включений в литниковые чаши или другие элементы литниковой системы иногда устанавливают фильтры (например, керамические сетки). С их помощью можно, отделить относительно крупные шлаковые частицы.
Чрезвычайно перспективным способом тонкой очистки металлических расплавов в литниковых системах является фирам-процесс (фильтрационное рафинирование металлов), при котором фильтрующий узел делают из специальной стеклоткани (см. рис. 196). При фирам-процессе значительно повышается чистота металла и, как следствие, качество отливок, уменьшается брак, что в целом дает значительный экономический эффект. Этот способ используют на многих предприятиях для отливок из серого и высокопрочного чугуна, бронзы и других сплавов.
Прибыли
рис. 198. Прибыли: а — открытая коническая; 6 — закрытая полушаровая; в — закрытая шаровая; г - работающая под атмосферным давлением; д — работающая под газовым давлением; с — легкоотделяемая |
Назначение прибылей — получение отливок без усадочных раковин и пористости, которые могут образовываться вследствие уменьшения объема расплава при его затвердевании. Прибыли размещают у массивных частей отливки, где усадка проявляется наиболее значительно.
Прибыли различают по их геометрической форме, месту расположения, условиям питания металлом тела отливки и т. д. Выбор рациональной прибыли зависит от формы, размеров, массы отливки, усадки сплава и других условий. Правильность расчета прибылей проверяют экспериментальными исследованиями структуры металла. Некоторые типы прибылей показаны на рис. 198.
• Открытые прибыли прямого питания применяют для крупных стальных отливок, производя иногда добивку, по мере снижения уровня металла. Такая прибыль служит также выпором, в нее могут всплывать частицы формовочной смеси и другие загрязнения.
Во многих случаях применяют закрытыеприбыли, дающие экономию металла. Например, для ответственных стальных отливок с массой 100—500 кг и толщиной стенок до 30мм технологический выход годного составляет при открытых прибылях 56—64%, при закрытых 61—69%. Наименьший необходимый объем имеют прибыли шаровой формы, наибольший — конической.
В закрытых прибылях, действующих под атмосферным давлением, создаются благоприятные условия для образования выгодно расположенных усадочных раковин и обеспечения плотной структуры отливки. Атмосферное давление создают, устанавливая в полость прибыли специальные газопроницаемые стержни из песчано-масляных смесей.
Прибыли, действующие под давлением газов, впервые разработаны советскими исследователями П. И. Яшмановым, А. А. Рыжиковым и др. В полость прибыли помещают в специальном патроне заряд газотворного вещества, обычно мел с добавками кокса. Патрон устроен так, что заряд начинает разлагаться после образования на поверхности прибыли тонкой твердой корочки металла. Выделяющиеся газы создают давление, вытесняя жидкий металл в тело отливки.
Для получения легко отделяемых прибылей (приоритет П. А. Иванова) применяют разделительные пластины (стержни-пластины, стержни-диафрагмы), например, как показано на рис. 198, е, которые изготовляют из шамотно-глинистых смесей.
Ручная формовка
Основной способ изготовления форм в отечественном литейном производстве — машинная формовка. Доля ручной формовки составляет менее 8% отливок по массе и непрерывно сокращается.
Ручная формовка связана с тяжелой и трудоемкой работой, что приводит к низкой производительности. Этот способ формовки еще находит некоторое применение для получения мелких и средних отдельных отливок или небольшой их партии. Более важное значение ручная формовка имеет в производстве крупных отливок в почву (в кессонах), формы для которых трудно или невозможно изготовить методами машинной формовки.
5 в г |
Рис. 199. Схема формовки в Двух опоках по разъемной модели а- модель; 6, в - изготовление нижней и верхней полуформ, г —собранная форма;1 — вентиляционные накалы; 2 —нижняя опока; 3 - нижняя половина модели; 4 — подмодельный щиток; 5 — модель стояка; 6 — модели выпоров; 7 — верхняя половина модели; 8 —верхняя опока; 9— стержень |
Формовка в двух опоках по разъемной модели - наиболее распространенный способ ручной формовки в производстве мелких и средних отливок - показана на рис. 199.
Для изготовления нижней полуформы на подмодельный щиток устанавливают половину модели 3, опоку 2, засыпают и уплотняют трамбовкой сначала облицовочную, а затем наполнительную смесь; в уплотненной смеси специальной иглой делают газоотводные (вентиляционные) наколы. Затем опоку поворачивают на 180°, устанавливают по шипам вторую половину модели, модели стояка и выпора. После
в г |
уплотнения смеси делают вентиляционные наколы и вынимают модели стояка и выпора; затем опоку снимают и вынимают половинки модели (специальным приспособлением).
Рис. 200. Схема формовки по шаблону: а — изготовление модели из формовочной смеси; 6-изготовление верхней полуформы в опоке; в-собранная форма; г – отливка. |
В нижней полуформе прорезают питатель — канал, соединяющий стояк литниковой системы с телом отливки. Для удаления случайных частиц формовочной смеси полуформы обдувают воздухом и на их внутреннюю поверхность наносят тонкий слой припыла (для сухих форм — формовочной краски). При сборке формы в нее устанавливают отдельно изготовленный стержень.
Формовка по шаблону также находит некоторое применение в производстве отдельных средних и крупных отливок относительно простой формы, поверхности которых можно оформить вращением шаблона — профильной доски. Сущность изготовления формы поясняет рис. 200.
В уплотненной формовочной смеси вращением шаблона оформляют наружную поверхность отливки и используют ее как модель для формовки в опоке верхней полуформы. Затем удаляют опоку, вторым шаблоном оформляют нижнюю полуформу, снимая слой смеси, равный толщине стенки отливки.
Машинная формовка
а Рис.201. Схема верхнего (а) и нижнего (б) прессования |
Машинная формовка обеспечивает не только современное массовое, крупносерийное, серийное производство; во многих случаях ее успешно используют для получения мелких серий или даже отдельных отливок. Применение машинной формовки во много раз увеличивает производительность труда, улучшает качество форм, а следовательно, и отливок, снижает брак, облегчает условия работы формовщика. Совершенствование формовочных машин привело к созданию полуавтоматических и автоматических формовочных установок, поточных и автоматических линий.
По характеру уплотнения смеси различают машины прессовые, встряхивающие и др.
Уплотнение прессованием может осуществляться по различным схемам, выбор которых зависит от размеров, формы модели, требуемой степени и равномерности уплотнения формовочной смеси и других условий.
В машинах с верхним прессованием (рис. 201, а) уплотняющее давление действует сверху. На столе машины 1 закрепляют модельную плиту 2 с моделью 3, устанавливают опоку 4 и на нее наполнительную рамку 5. Опоку и рамку заполняют формовочной смесью из бункера. При подъеме стола прессовая колодка 6 входит в наполнительную рамку, запрессовывая смесь в опоку; высота наполнительной рамки определяет вытесняемый объем формовочной смеси, а следовательно, и степень ее уплотнения в опоке. После завершения прессования стол с модельной оснасткой опускают в исходное положение.
В машинах с нижним прессованием (рис. 201, б) формовочная смесь уплотняется самой моделью и модельной плитой. Удельное давление при прессовании обычно составляет 300—500 кПа.
Рис. 202. Схемы прессования: а —профильной колодкой, б — дифференциальное; в - эластичной мембраной; 1-стол машины: 2-опока; 3— модель; 4- прессовая колодка; 5-рамка |
Недостатком этих способов прессования является неравномерность уплотнения формовочной смеси. При верхнем прессовании наиболее уплотнены верхние слои смеси, наименьшая степень уплотнения у поверхности модели. При нижнем прессовании наиболее уплотнена смесь у поверхности модели, что обеспечивает получение более качественной формы. Несмотря на это, чаще применяют машины с верхним прессова-
-нием. Машины с нижним прессованием имеют более сложное устройство и менее надежны в эксплуатации.
Неравномерность уплотнения смеси возрастает с увеличением высоты опоки. Поэтому уплотнение прессованием применяют для изготовления полуформ в невысоких опоках (до 200—250мм). Этот недостаток может быть устранен применением профильных колодок (рис. 202, а), дифференциальным прессованием с вдавливанием в смесь нескольких колодок (рис. 202, б). Равномерное уплотнение смеси можно получить также прессованием с диафрагмой — эластичной резиновой мембраной (рис. 202, в). Смесь уплотняется, например, давлением сжатого воздуха через эластичную мембрану, повторяющую рельеф поверхности модели.
Прессование под высоким давлением (до 4 МПа) сравнительно новый, прогрессивный способ формовки. Этот способ дает возможность изготовлять полуформы с требуемой степенью уплотнения в высоких опоках (до 350мм), с повышенной точностью по размерам и гладкой поверхностью. При высокой степени уплотнения повышается теплопроводность смеси, что способствует улучшению структуры металла в отливке.
Уплотнение встряхиванием получило широкое применение в литейном производстве. На встряхивающих машинах уплотнение происходит в результате многократно повторяемых встряхиваний. Принципиальная схема встряхивающей машины показана на рис. 203, а. На столе 1 укрепляют модельную плиту с моделью 2,
устанавливают опоку 3 и наполнительную рамку 4. Под давлением
сжатого воздуха, поступающего через каналы 5, стол поднимается
на высоту 30—100мм (рис.203,б), определяемую положением
выпускного отверстия 6. Вследствие понижения давления подвиж-
ные части падают вниз. При ударе стола по торцовой поверхности
направляющего цилиндра смесь уплотняется в результате появления инерционных сил
Уплотнение смеси происходит неравномерно. Дополнительное уплотнение верхних рыхлых слоев смеси осуществляют допрессовкой.
На некоторых заводах применяют другой комбинированный способ — совмещение встряхивания с подпрессовкой.
При включении встряхивающего стола на слой формовочной смеси, выступающей под опокой, накладывают тяжелую подпрессовочную плиту. Такой способ повышает время набивки смеси и качество ее уплотнения. Встряхивание машины дают возможность уплотнения смеси в высоких опоках, изготавливать формы по сложным моделям с высокими ребрами и впадинами. Режим уплотнения: подъем стола 30—100 мм, число ударов 30— 50 в мин. Для уплотнения смеси в опоке 1200x800х460 мм для крупной отливки требуется 25—50 ударов, время уплотнения 25—40 с (время допрессовки 2—5 с). В нашей стране созданы уникальные встряхивающие машины, обеспечивающие формовку очень крупных отливок (до 15 т) в опоках размерами до 2500х2000 мм. Основными недостатками встряхивающих машин являются меньшая производительность, чем у прессовых машин, а также сильный шум при работе.
Вакуумная формовка (иногда ее называют пленочно-ваку- умной формовкой). Сущность ее заключается в следующем (рис. 204).
Рис. 206. Схема устройства метательной головки пескомета: ' — метательный ковш; 2 — подача формовочной смеси 3 —кожух головки; 4 — отверстие для выброса смеси я опоку |
Вакуумирование продолжается не только при изготовлении полуформ, но и при их сборке, заливке и затвердевании залитого металла. При заливке металла в форму пленка сгорает. Продукты сгорания выполняют роль противопригарного покрытия.
Этот способ имеет целый ряд преимуществ, в том числе удешевление формовочной смеси и упрощение смесеприготовления, повышение точности отливок и улучшение чистоты их поверхности, упрощение выбивки форм, удлинение срока службы оснастки и др.
Процесс позволяет получать отливки из различных сплавов массой 0,1—10 т. Формовка может быть ручной или на автоматических линиях.
Пескометы — высокопроизводительные формовочные машины — используют преимущественно для изготовления форм крупных отливок в опоках ив кессонах. Особенность формовки состоит в том, что пескомет обеспечивает одновременно две операции: засыпку смеси и ее уплотнение.
Основной частью пескомета является его метательная головка (рис. 205). Формовочную смесь, поступающую в головку пескомета по транспортеру, подхватывают метательные ковши (лопасти), вращающиеся с частотой до 1500 мин-1, и выбрасывают со скоростью 30—60 м/с через отверстие в опоку. Из-за большой скорости выброса формовочная смесь хорошо и равномерно уплотняется в опоках любой высоты. Для направления струи формовочной смеси головку можно перемещать в горизонтальной и вертикальной плоскостях.
Производительность пескометов обычно не менее 10—15 м3/ч.
Извлечение моделей из форм при формовке вручную — ответственная операция, требующая определенного навыка в работе. Модель предварительно «расталкивают» легкими ударами, а затем осторожно извлекают при помощи крючка или ввернутого болта. При машинной формовке эта операция механизирована, что обеспечивает сохранение точных размеров и отсутствие повреждений форм.
Рис. 206. Схема устройства механизмов для удаления моделей из форм: а — подъемом опоки; б - опусканием модели через протяжную плиту; в- поворотной плитой; 1 - модель; 2 - опока; 3 - модельная плита; 4 — протяжная плита; 5- поворотный стол; 6-штифтовый механизм |
На рис. 206, а показано извлечение невысокой модели. Опоку поднимают при помощи штифтов подъемного механизма, а модельная плита (модель) остается на месте. Модель большой высоты опускают вниз через протяжную плиту, заформованная опока остается на месте (рис. 206, б).
Часто модели извлекают при помощи поворотной плиты. Эту плиту прочно скрепляют с опокой и модельной плитой и поворачивают на 180°. Затем опоку освобождают и опускают вниз или поднимают модель вверх (рис. 206, в).
Технология машинной формовки
Формовка в двух опоках (рис. 207) является наиболее распространенным способом. Модельную плиту с моделью обдувают воздухом для удаления пыли и опрыскивают керосином, чтобы не прилипала формовочная смесь. Затем устанавливают нижнюю опоку и заполняют ее формовочной смесью из бункера, расположенного над машиной. После уплотнения смеси прессованием или другим способом удаляют ее излишек. На опоку устанавливают щиток, поворачивают ее на 180° и вынимают модель.
Аналогичным образом формуют верхнюю полуформу. При сборке формы в нижнюю полуформу устанавливают стержень и обдувают сжатым воздухом для удаления пыли. Затем по направляющим штырям устанавливают верхнюю полуформу, скрепляют обе опоки скобами или другим способом и направляют к месту заливки.
Безопочная формовка на формовочных машинах и высокопроизводительных полуавтоматических установках (200—300 форм/ч) широко применяется в массовом производстве мелких изделий.
Этот способ формовки можно выполнять по различным вариантам. Основные операции формовки в двух опоках с двусторонней модельной плитой показаны на рис. 208.
На нижнюю опоку по штырям устанавливают модельную плиту и верхнюю опоку. Затем сборку поворачивают на 180° и изготовляют нижнюю полуформу; далее накладывают подопочный щиток, поворачивают сборку на 180° и уплотняют смесь в верхней опоке. После этого снимают верхнюю опоку и удаляют модельную плиту. После сборки полуформ обе опоки снимают, на форму надевают тонкостенный металлический
кожух-жакет для предохранения от разрушения. Для изготовления форм требуется ограниченное число опок, что дает большую экономию.
При безопочной формовке по схеме, приведенной на рис. 209, формовочную смесь из бункера подают сжатым воздухом в рабочий резервуар. Уплотнение смеси происходит при перемещении модельной плиты штоком 3. Затем поворотную модельную плиту поднимают вверх. Полуформу перемещают штоком в положение 6. Из полуформ образуются безопочные формы.
Стопочная формовка (этажная и ступенчатая) (рис. 210) применима в литейных цехах, где формы заливают не на конвейерах, а на специальной площадке. При этажной формовке формы для небольших отливок простой конфигурации изготовляют, например, на прессовых машинах таким образом, чтобы в одной опоке была получена нижняя полуформа с одной стороны и верхняя полуформа с дру-
Pug. 208. Безопочная формовка: |
![]() |
Рис. 210, Схема стопочкой формовки: слева — этажная; оправа ™ стопорная формовка; 1 — общий литниковый стояк; 2 — полости форме 3 «— опоки; 4 — подопечный щиток? 5- литниковый стояк |
Рис. 211. Изготовление форм в стержнях: а — в опоках; б - о применением жакета; 1-нижняя опока, 2 - жакет; 3 - верхняя опока; 4 - прибыль;- 5 — отливка |
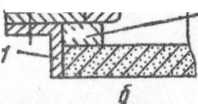
— |
Изготовление форм в стержнях (формовку в стержнях) применяют для получения тонкостенных отливок сложной конфигурации или при наличии тонких выступающих ребер, как экономически более выгодный способ изготовления форм, чем формовка по моделям. При этом способе наружные и внутренние поверхности отливки получают в форме, собранной из стержней (рис. 211, а). Формовка в стержнях упрощает изготовление формы,увеличивает производительность труда; отливки получают о чистыми поверхностями, минимальными допусками и припусками на механическую обработку. Более широкое применение этого способа стало возможным с применением ЖСС и других специальных смесей.
![]() |
Комплект стержней, чтобы предупредить его разрушение при заливке, скрепляют скобами, помещают в опоки или жакеты —чугунные ящики; в последнем случае этот способ называют формовкой в жакетах (макетная формовка).
Формовка в жакетах находит применение и в серийном производстве крупных отливок. На рис. 211, б показано использование жакета для получения средней части формы, верхняя и нижняя части которой выполнены в опоках. Такой способ дает возможность изготовить формы большей высоты, чем при обычной машинной формовке в опоках. Для особо крупных отливок формовку в стержнях ведут в кессонах.
Изготовление форм в кессонах проводят для крупных отливок, например, с массой более 10 т и с размерами более 2,5 м; некоторые отливки имеют массу до нескольких десятков тонн, длину 10— 15м и более. Для таких отливок формы в опоках изготовить нельзя, их изготавливают в кессонах формовкой вручную, в стержнях, с применением жидких самотвердеющих смесей и др.
Рис. 212. Сборка формы из стержней — блоков в механизированном кессоне. |
Кессон — железобетонная яма, расположенная ниже уровня пола цеха, водонепроницаемая для грунтовых вод. Современный механизированный кессон имеет две неподвижные и две подвижные стенки из чугунных плит, что позволяет изменять его размеры. Его дно выкладывают из полых чугунных плит, которые можно продувать воздухом для ускорения охлаждения отливки и кессона. Кессон имеет механизмы для передвижения стенок, приспособления для установки и закрепления верхней полуформы.
Формовка вручную в почве обычно выполняется в кессонах. Для крупных отливок нижняя часть формы испытывает большое давление и должна иметь хорошую газопроницаемость. Поэтому в нижней части кессона делают «твердую постель», уплотняя скачала формовочную смесь, затем слой твердой засыпки (куски кокса, шлака, огнеупорного кирпича и т. п.) и снова слои наполнительной и облицовочной смеси. Для отвода газов в слое твердой засыпки устанавливают вентиляционные трубы.
На подготовленную постель помещают модель и набивают остальную часть формы. Уплотнение формовочной смеси является наиболее сложной, ответственной и трудоемкой операцией. Смесь уплотняют пневматическими трамбовками, могут быть использованы и пескометы. Наибольшие затруднения вызывает уплотнение смеси под моделью; набивку труднодоступных мест выполняют через специальные окна в модели.
Формовка в кессонах с применением ЖСС позволяет значительно упростить технологию изготовления форм для крупных отливок при одновременном улучшении их качества. На рис. 213 приведен пример изготовления формы с применением ЖСС для крупной чугунной отливки. После фиксации модели 2 планками 3 через круглые или квадратные отверстия 5 заливают ЖСС и затем выдавливают ее толкателями 4 для лучшего заполнения подмодель-ного пространства. Далее заливают формовочную смесь по периферии в зазоры между стенками модели и кессона /. Во избежание всплывания при заливке модель нагружают. Через 30—40 мин модель извлекают, форму окрашивают противопригарной краской, сушат 2—4 ч (переносными газовыми сушилами). Вследствие высокой газопроницаемости смеси отвод газов значительно упрощается по сравнению с формовкой в почве. Газоотвод может быть обеспечен, например, прокладкой в слой смеси системы Трубок из нейлона или других синтетических материалов.
Из песчано-глинистых смесей такую форму изготовить невозможно, так как нельзя обеспечить уплотнение смесей под моделью.