Расчет зубьев червячного колеса на изгиб
£ [d]F МПа, где Ye – коэффициент, учитывающий суммарную длину контактных линий, Yd – коэффициент, учитывающий угол охвата, Yg – коэффициент, учитывающий форму зуба (зависит от приведенного числа зубьев ZV), K – коэффициент нагрузки.
В передачах с большим передаточным числом (больше 70), а также открытые передачи при проектировании рассчитываются по изгибной прочности зубьев (по модулю):
Допускаемое напряжение изгиба определяется из условия предотвращения усталостного излома зубьев. Расчет [d]F базируется на кривых усталости:
[d]Fm × N = const, m=9
[d]F = (dFO / SF) ×KFL, где dFO – реверсивные нагрузки, SF – коэффициент безопасности, KFL – коэффициент долговечности
NFE – эквивалентное число циклов, NHO – базовое число циклов.
NFE = NS×m9,
NS = 60× n2 × Lh – суммарное число циклов.
21) Червя́чная переда́ча (зубчато-винтовая передача) — механическая передача, осуществляющаяся зацеплением червяка и сопряжённого с ним червячного колеса.
Достоинства:
Плавность работы
Бесшумность
Большое передаточное отношение в одной паре
Самоторможение
Повышенная кинематическая точность
Недостатки:
Сравнительно низкий КПД (целесообразно применять при мощностях не более 100 кВт)
Большие потери на трение (тепловыделение)
Повышенный износ и склонность к заеданию
Повышенные требования к точности сборки, необходимость регулировки
Необходимость специальных мер по интенсификации теплоотвода
По числу витков червяки делят на однозаходные и многозаходные, по направлению витка — левые или правые. Наиболее распространено правое направление с числом витков червяка , зависящим от передаточного числа ; выбирают так, чтобы обеспечить число зубьев колеса : .
Материалы червячной передачи.
Материалы в червячной передаче должны иметь в сочетании низкий коэффициент трения, обладать повышенной износостойкостью и пониженной склонностью к заеданию. Обычно это разнородные материалы.
Червяки изготовляют в основном из сталей марок 40, 45, 50 (реже из сталей 35, Ст5) с закалкой до HRC 45-55; 15Х, 20Х, 40Х, 40ХН, 12ХНЗ, 18ХГТ с цементацией и закалкой до HRC 58—63.
Червячные колеса (или их венцы) изготовляют только из антифрикционных сплавов.
При больших диаметрах колес чугуны марок СЧ15, СЧ20, СЧ25;
В зависимости от способа соединения венца с центром различают следующие конструкции червячных колес:
1. С напрессованным венцом — бронзовый венец насажен на стальной центр с натягом. Такую конструкцию применяют при небольших диаметрах колес в мелкосерийном производстве.
2. С привернутым венцом — бронзовый венец с фланцем крепят болтами к центру. Фланец выполняют симметрично относительно венца для уменьшения деформаций зубьев. Эту конструкцию применяют при больших диаметрах колес ( мм).
3. С венцом, отлитым на стальном центре — стальной центр вставляют в металлическую форму (кокиль), в которую заливают бронзу для получения венца. Эту конструкцию применяют в серийном и массовом производстве.
Крепление венца к ступице должно обеспечивать фиксацию как от проворота (осевая сила червяка = окружной силе колеса), так и от осевого "снятия" венца (окружная сила червяка = осевой силе колеса).
22) см .21 + Одной из причин повышенного изнашивания зубьев червячного колеса (и заедания) является скольжение витков червяка по зубьям червячного колеса при отсутствии разделяющей их масляной пленки. Скорость скольжения направлена по касательной к винтовой линии делительного диаметра червяка и определяется из параллелограмма скоростей
где и — окружные скорости червяка и колеса, м/с; , мм; - угловая скорость червяка, рад/с.
Основные силовые зависимости - ?
19) Конические зубчатые колёса применяют в передачах, оси валов которых пересекаются под некоторым межосевым углом . Обычно сумма углов равна 90’
Параметры - ?
24) Сварное соединение - неразъемное соединение, выполненное сваркой. Сварное соединение : зону сварного шва 1, зону сплавления 2, зону термического влияния 3, а также часть основного металла 4, прилегающую к зоне термического влияния.
Сварной шов - участок сварного соединения, образовавшийся в результате кристаллизации расплавленного металла.
Металл шва - сплав, образованный расплавленным основным и наплавленным металлами или только переплавленным основным металлом.
Основной металл - металл подвергающихся сварке соединяемых частей.
Зона сплавления - зона, где находятся частично оплавленные зерна металла на границе основного металла и металла шва. Эта зона нагрева ниже температуры плавления. Нерасплавленные зерна в этой зоне разъединяются жидкими прослойками, связанными с жидким металлом сварочной ванны и в эти прослойки имеют возможность проникать элементы, введенные в ванну с дополнительным металлом или сварочными материалами. Поэтому химический состав этой зоны отличен от химического состава основного металла.
Зона термического влияния - участок основного металла, не подвергшийся расплавлению, структура и свойства которого изменились в результате нагрева при сварке, наплавке или резке.
Тип сварного соединения
Стыковое соединение - сварное соединение двух элементов, примыкающих друг к другу торцовыми поверхностями и расположенных в одной плоскости или на одной поверхности.
Угловое соединение - сварное соединение двух элементов, расположенных под углом и сваренных в месте примыкания их краев
Тавровое соединение - сварное соединение, в котором торец одного элемента примыкает под углом и приварен к боковой поверхности другого элемента
Нахлесточное соединение - сварное соединение, в котором сваренные элементы расположены параллельно и частично перекрывают друг друга (рис. 1.5, а, б). Отсутствие опасности прожогов при сварке облегчает применение высокопроизводительных режимов сварки. Применение нахлесточных соединений облегчает сборку и сварку швов, выполняемых при монтаже конструкций (монтажных швов).
Торцовое соединение - сварное соединение, в котором боковые поверхности сваренных элементов примыкают друг к другу (рис. 1.5, е).
РАЗРУШЕНИЕ СВАРНЫХ ШВОВ
25) Резьбовое соединение — разъёмное соединение деталей машин при помощи винтовой или спиральной поверхности (резьбы). Это соединение наиболее распространено из-за его многочисленных достоинств. В простейшем случае для соединения необходимо закрутить две детали, имеющие резьбы с подходящими друг к другу параметрами.
Достоинства:
технологичность;
взаимозаменяемость;
универсальность;
надёжность;
массовость.
Недостатки:
раскручивание (самоотвинчивание) при переменных нагрузках и без применения специальных устройств (средств).
отверстия под крепёжные детали как резьбовые так и гладкие вызывают концентрацию напряжений.
для уплотнения (герметизации) соединения необходимо использовать дополнительные технические решения.
Примечание: коническая резьба обладает свойством герметичности и самостопорения.
Резьба имеет следующие основные геометрические параметры:
наружный диаметр — d, D;
внутренний диаметр — d1, D1;
средний диаметр — d2, D2 (диаметр воображаемого цилиндра, на поверхности которого толщина витка равна ширине впадины);
шаг резъбы — р (расстояние между соседними одноименными боковыми сторонами профиля в направлении, параллельном оси резьбы);
число заходов — n (заходность резьбы легко определяется на торце винта по числу сбегающих витков);
угол подъема резьбы — угол, образованный касательной к винтовой линии резьбы в точках, лежащих на среднем диаметре, и плоскостью, перпендикулярной оси резьбы
h – рабочая высота профиля, по которой соприкасаются боковые стороны резьб винта и гайки
ph – ход винта для многозаходных резьб, равный произведению шага на число заходов; – угол профиля; – угол подъема (угол подъема развертки винтовой линии по среднему диаметру), который определяется как
.
Профиль резьбы зависит от формы режущей части инструмента, с помощью которого нарезается резьба. Чаще всего применяется цилиндрическая треуголь ная резьба. обычно ее называют крепежной, так как нарезают на крепежных деталях, например на шпильках, болтах и гайках. Рис. 3. Виды резьб в зависимости от профиля:
а — цилиндрическая треугольная, б — прямоугольная, в — трапецеидальная, г - упорная, д – круглая
Конические треугольные резьбы дают возмож ность получить плотное соединение. Такие резьбы встречаются на кони ческих пробках, иногда — в масленках.
Прямоугольная резьба (рис. 3,б) имеет прямоуголь ный (квадратный) профиль. Она не стандартизована, трудна в изготовле нии, непрочная и применяется редко.
Трапецеидальная ленточная резьба (рис. 3,в) имеет сечение в виде трапеции с углом профиля, равным 30°. Коэффици ент трения у нее мал, поэтому она применяется для передачи движений или больших усилий в металлорежущих станках (ходовые винты), дом кратах, прессах и т. п. Витки этой резьбы имеют большое сечение у осно вания, что обеспечивает ее высокую прочность и удобство при нарезании. Основные элементы трапецеидальной резьбы стандартизованы.
Упорная резьба (рис. 3, г) имеет профиль в виде неравно-бокой трапеции с рабочим углом при вершине, равным 30°. Основания витков закруглены, что обеспечивает в опасном сечении прочный профиль. Поэтому данная резьба применяется в тех случаях, когда винт дол жен передавать большое одностороннее усилие (в винтовых прессах, домкратах и т. п;).
Круглая резьба (рис. 3,д) имеет профиль, образованный двумя дугами, сопряженными с небольшими прямолинейными участка ми, и углом, равным 30°. В машиностроении эта резьба используется редко, Эта резьба не стандартизована.
Виды Соединений:
резьбовое соединение при непосредственном скручивании соединяемых деталей (резьба имеется на этих деталях);
резьбовое соединение при помощи дополнительных соединительных деталей, например, болтов, шпилек, винтов, гаек и т.д;
болтовое соединение; (Болтовое соединение, распространённый тип резьбового соединения болтом и гайкой. Обычно в отверстие соединяемых деталей болт вставляется с зазором (рис.), и соединение осуществляется затяжкой гайки, что создаёт давление между деталями, препятствующее их расхождению (раскрытию стыка) под действием осевых сил (Р) и относительному сдвигу под действием поперечных сил (Q), благодаря возникающему между деталями трению)
винтовое соединение; ( резьбовое соединение деталей винтами. В отличие от болтового соединения и крепления деталей шпильками, не нуждается в гайках, так как резьба выполняется в самой детали.)
шпилечное соединение.
Болтовое соединение это соединение деталей с помощью болта.Шпилечное- с помощью шпильки.Разница между болтом и шпилькой очевидна:болт имеет головку под ключ и резьбу,шпилька имеет резьбу с обеих сторон и закрепляет деталь гайкой..
Болт - это крепежная деталь, представляющая собой цилиндрический стержень с головкой и наружной резьбой. Если резьба не по всей длине болта, то диаметр в той его части, где нет нарезки, примерно такой же, как и диаметр резьбы, измеренный на вершинах ее витков. Головка болта по форме может быть квадратной, шестигранной, цилиндрической, конической, эллиптической или овальной.
Гайка - металлическая деталь, имеющая обычно квадратную или шестигранную форму, с отверстием в центре. Внутри отверстия имеется резьба, соответствующая резьбе стандартного болта. Гайки бывают различные - стопорные, с продольными шлицами, корончатые, крыльчатые и т.д.
Часто при сборке изделий принимаются, меры к стопорению резьбовых соединений. Вызвано это тем, что от толчков и сотрясений, которые неизбежны при работе любой машины, может произойти самоотвинчивание резьбовых соединений.
Стопорение контргайкой (рис. 143, I), осуществляется за счет трения, возникающего в резьбе и на торцовых поверхностях гаек. Основным недостатком этого способа является утяжеление соединения.
Стопорение пружинной шайбой (рис. 143, II), основано на том, что пружинная шайба создает дополнительное напряжение в резьбовом соединении, и, кроме того, острые закаленные кромки шайбы, врезаясь в опорную поверхность гайки, предотвращают тем самым ее самоотвинчивание.
Стопорение винтом, ввинченным в гайку (рис. 143, III), — способ, позволяющий стопорить гайку в любом положении. Для того чтобы не отвинчивался сам стопорный винт, шаг его резьбы должен быть по возможности мал. Недостаток этого способа заключается в том, что часть резьбы болта сминается стопорным винтом.
Стопорение штифтом коническим разводным (рис. 143, IV) — простой и надежный способ. После затяжки гайки ее просверливают вместе с болтом. В отверстие вставляют конический штифт и разводят его концы.
Стопорение разводным шплинтом (рис. 143, V, VI) — один из наиболее надежных способов. Шплинт изготовляют из стальной проволоки полукруглого сечения. Он имеет головку в виде кольца. Отверстие в болте под шплинт просверливают до или после монтажа. Разводной шплинт вставляют в это отверстие и в пазы корончатой или прорезной гайки.
Стопорение деформируемыми шайбами широко применяют в технике. Существует много конструкций деформируемых и фигурных шайб, некоторые из них приведены на рис. 143, VIII—XI. Обычно один ус шайбы отгибают по краю детали, а другой — по грани гайки. Применяют и фигурные шайбы, которые наподобие вилки обхватывают грани гайки.
29) Высота гайки выбирается H=0.8d, d – наружний диаметр винта.
ИсследованиямиЖуковского установлено, что нагрузка по виткам распределяется неравномерно(рис. 8.6). Это связано с характером деформации стержня и гайки. Первый отопорной поверхности гайки виток стержня болта имеет наибольшее перемещение(на величину удлинения стержня между крайними витками) по мере удалениявитка от опорной поверхности перемещение витка будет уменьшаться. Гайка поддействием силы будет сжиматься, поэтому первый от опорной поверхности витокбудет иметь минимальное перемещение, так как высота участка сжатия минимальная. Разность перемещений первых витков стержня и гайки будетмаксимальной. По закону Гука нагрузка пропорциональна деформации, то ест первый воспринимае максимальную часть.По мере удаления от опорной поверхности разность деформаций будет уменьшаться, следовательно и нагрузка на виток будет меньше. Для выравнивания нагрузки между витками необходимо сделать так, чтобы гайка также испытывала растяжение.при расчете резьбы условно считают, что все витки нагружены одинаково, анеточность в расчете компенсируют значением допускаемого напряжения.Условие прочности резьбы на срез имеет вид
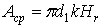
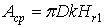







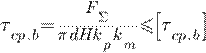
Условия прочности резьбы по напряжениям среза:
Болта Гайки
где FΣ — суммарное осевое усилие, воспринимаемое резьбой и определяемое в зависимости от видов нагружения резьбового соединения, но без коэффициента 1,3, учитывающего скручивание стержня болта (винта, шпильки) при затяжке; kп — коэффициент полноты резьб: для треугольной kп= 0,87; для трапецеидальной kп = 0,65; для прямоугольной kп = 0,5; km — коэффициент неравномерности распределения нагрузки между витками; km = 0,6...0,7; [τср.б] и [τср.г] — соответственно допустимое напряжение на срез резьбы болта и гайки.
Если материалы болта и гайки одинаковые, то по напряжению среза рассчитывают только резьбу болта, так как d1< d
Расчёт незатянутого болта при действии осевой силы. Стержень болта работает только на растяжение (рис. 4.3.21).
Проектировочный расчёт выполняют по формуле где dp – минимальный расчётный диаметр болта,
F0 – внешняя осевая сила.
Диаметр резьбы определяется по формуле:
d=dp+0,94p
где р – шаг резьбы,
d – наружный диаметр резьбы
Расчет незатянутых болтов. Характерный пример незатянутого резьбовогосоединения — крепление крюка грузоподъемного механизма.Опасным в резьбовом стержне является сечение нарезанной части с расчетным диаметром
Условие прочности для этого случая
где F — осевая нагрузка; — расчетный диаметр резьбы;
— допускаемое напряжение на растяжение.Из формулы
определяем расчетный диаметр резьбы:
Расчет затянутых болтов. Таким образом, вместо расчета резьбового соединения на растяжение и кручение можно произвести расчет только на растяжение, принимая не заданное усилие затяжки, а в 1,3 раза больше, т. е.
где
— расчетная (эквивалентная) нагрузка,
Из условия прочности определяется расчетный диаметр резьбы по формуле
31) Расчет затянутого резьбового соединения, не нагруженного внешней осевой силой
Примером такого соединения может служить крепление люков, крышек, к герметичности которых не предъявляются особые требования. Другим примером является клеммовое соединение.
Под действием момента, создаваемого усилием на рукоятке ключа, резьбовое соединение получает затяжку. Стержень с резьбой растягивается усилием затяжки и скручивается моментом в резьбе. При одновременно действующих осевой силе и скручивающем моменте, возникающем в процессе затяжки болта, болт следует рассчитывать на прочность по приведенному (эквивалентному) напряжению. В среднем для метрическихрезьб приведенное напряжение больше напряжения растяжения примерно на 30 %.
Таким образом, вместо расчета резьбового соединения на растяжение и кручение можно произвести расчет только на растяжение, принимая не заданное усилие затяжки, а в 1,3 раза больше, т. е.
где F0— расчетная (эквивалентная) нагрузка,F0=1.3F
Из условия прочности определяется расчетный диаметр резьбы по формуле
2 Расчет болтовых соединений, выполненный с предварительной затяжкой.(при действии сил, открывающих детали).
1.Определение податливости болта и деталей.
Деформирование болта с усилием растяжения законом Гука.
- податливость болта
или
Длина болта – толщина соединения деталей; у винта – толщина детали, в которой резьба не нарезана.
- площадь поперечного сечения болта.
и
Деформирование деталей определяется по конусам влияния ( конусами Бабарыкова)
Конус влияния можно заменить цилиндром, если
![]() |
![]() |
2.Рассмотрим зависимость деформации болтового соединения от прилагаемой нагрузки:
а) болт не нагружен осевой силой, затяжки нетб) к болту прикладывают силу затяжки (болт вытягивается, а деталь сжимается на и
соответственно).
Деформация болта и детали рассматриваем совместно. В случае затяжки .в) затянутое соединение подвергается действию силы Fa, открывающей детали.
Болт вытягивается на а деталь разжимается на эту же величину.
Fa– доля внешней силы, которая приходится к растяжению болта
- коэффициент внешней нагрузки (показывает долю внеш-ней нагрузки, приходящейся на болт).
- доля внешней силы, приходящейся на деталь
Fоз– сила остаточной затяжки.
Выведем условное отсутствие открытия стыка.
Fоз>0 сила затяжки тогда определяется в зависимости от осевой силы Fa:
к – коэффициентпредварительной затяжки (1,3-1,5)
FР =1,3FЗ + ![]() |
Общая сила растяжения болта: FР =FЗ + Fa,. Учитывая, что сила FЗпроизводит одновременно подкручивание болта, произведением домножения на 1,3:
![]() |
- проверочный расчет
расчетная формула
3. Определение коэффициента внешней нагрузки
При предварительных расчетах =0,2-0,3 (если нет между деталями податливой прокладки, иначе
= до 0,8)
Определение силы затяжки
Коэффициент внешней нагрузки – , учитывающий приращение нагрузки болта и уменьшение затяжки стыка, определяется по формуле:
32) Податливость винта (болта) и деталей. Податливость стержня постоянного сечения в общем виде определяется по формуле
где I — длина деформированной части детали; А — ее поперечное сечение; Ε — модуль упругости 1-го рода материала детали
λб = lб / (Еб Аб); λд = δд / (Ед Ад),где λб, λд— податливости болта и деталей, равные их деформации при единичной нагрузке (податливость обратна жёсткости); Еб, Ед, Аб, Ад — модули упругости и площади сечения болта и деталей; δд — суммарная толщина деталей δд ≈ lб.В сложном случае податливость системы определяют как сумму податливостей отдельных участков болта и отдельных деталей.
34) Шпоночное соединение – один из видов соединений вала со втулкой с использованием дополнительного конструктивного элемента (шпонки), предназначенной для предотвращения их взаимного поворота. Шпоночные соединения могут быть подвижными или неподвижными в осевом направлении
Классификация соединений в зависимости от формы шпонки: соединения призматическими шпонками, соединения клиновыми шпонками, соединения тангенциальными шпонками, соединения сегментными шпонками, соединения цилиндрическими шпонками
Призматические шпонки широко применяют во всех отраслях машиностроения. Простота конструкции и сравнительно низкая стоимость – главные достоинства этого вида соединений.
Отрицательные свойства: соединение ослабляет вал и ступицу шпоночными пазами;
Расчет ненапряженных
где h, b, l - высота, ширина и длина шпонки;
35) Под напряженнымпонимается такое соединение, в котором постоянно действуют внутренние силы упругости, вызванные предварительной (т.е. до приложения нагрузки) затяжкой.
Напряженные шпоночные соединения осуществляются стандартными круглой, клиновыми, тангенциальными шпонками с уклоном 1:100, обеспечивающим самоторможение.
Расчет напр.шпон. соед в тетради
36) Зубчатые соединения образуются при наличии наружных зубьев на валу и внутренних зубьев в отверстии ступицы (рис. 6.6). Размеры зубчатых соединений, а также допуски на них стандартизованы.
Зубья на валах получают фрезерованием, строганием или накатыванием. Зубья в отверстиях образуют протягиванием или долблением. Достоинства шлицевых соединений по сравнению со шпоночными: возможность передачи больших моментов благодаря значительной поверхности контакта соединяемых деталей и равномерному распределению давления по этой поверхности, более точное центрирование ступицы по валу, лучшее направление при перемещении ступицы по валу и большая прочность вала.
По профилю различают следующие шлицевые соединения (рис. 28):
прямобочные (а) - число шлиц Z = 6, 8, 10, 12;
звольвентные (б)- число шлиц Z = 12, 16 и более;
треугольные (в) - число шлиц Z = 24, 36 и более.
расчет на смятие, Τ — передаваемый вращающий момент, Η «мм; SF — удельный (на единицу длины) суммарный статический момент площади рабочих поверхностей, мм3/мм (см. табл. 5.1); /р— рабочая длина зубьев (см. рис. 5.1); [а]см — допускаемое напряжение смятия, Н/мм2.
37) Соединение с натягом — технологическая операция получения условно разъёмного соединения[1], которое получается при вставлении одной детали (или части её) в отверстие другой детали при посадке с натягом.
достоинствам цилиндрических соединений с гарантированным натягом относятся: простота конструкции, хорошее центрирование соединяемых деталей, возможность передачи больших нагрузок как статических, так и динамических (ударных).
Недостаткам цилиндрических соединений с гарантированным натягом относятся: сложность сборки и разборки соединений,
38) Заклёпочное соединение — неразъёмное соединение деталей при помощи заклёпок. Обеспечивает высокую стойкость в условиях ударных и вибрационных нагрузок.
По конструкции заклёпочные соединения делятся на однорядные и многорядные с цепным или шахматным расположением заклёпо
Достоинства Не позволяет распространяться усталостным трещинам, таким образом повышает надёжность всего изделия.
Позволяет соединять не поддающиеся сварке материалы.
Недосттатки ,Трудоёмкость процесса., Повышенная материалоёмкость соединения. Процесс сопровождается шумом и вибрацией.