Подбор корпусов и крышек подшипников, выбор уплотнений.
После выбора подшипника для него подбирают соответствующий корпус и крышки. Корпуса подшипников приводного вала рекомендуется принимать типа УМ по ГОСТ 13218.3-80 (рис.8 таб.8). Размер корпуса принимается по размеру наружного диаметра подшипника D.
Для D = 110 - 150 мм Для D = 80 – 100 мм
А |
2 отв. под штифт |
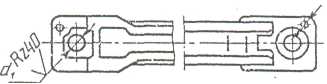
Б-Б |
2 отв. d2 под штифт конич. |
Рис. 8 Корпуса УМ подшипников качения (из ГОСТ 13218-80)
Таблица 8. Корпуса типа УМ подшипников качения по ГОСТ 13218.3-80, размеры, мм
Обозна-чение кор- пуса | УМ 80 | УМ 85 | УМ 90 | УМ 100 | УМ 110 | УМ 120 | УМ 125 | УМ 130 | УМ 140 | УМ 150 |
D | ||||||||||
D1 | ||||||||||
d | ||||||||||
d1 | ||||||||||
d2 | ||||||||||
d3 | ||||||||||
A | ||||||||||
B | ||||||||||
B1 | ||||||||||
L | ||||||||||
L1=D2 | ||||||||||
l | ||||||||||
H | 120,5 | 130,5 | 139,5 | 157,5 | 179,5 | 190,5 | 199,5 | |||
H1 | ||||||||||
h | ||||||||||
r | - | |||||||||
r1 | 12,5 | - |
Пример условного обозначения корпуса типа УМ, исполнения 1, D = 90 мм
Корпус УМ 90 ГОСТ 13218.3 – 80
Подшипниковые узлы обычно закрываются крышками, в которые встраиваются уплотнения. Для вышеприведенных корпусов, выбранных из ГОСТ 13218.3 – 80, рекомендуется выбирать стандартные крышки по ГОСТ 13219.1-81 - ГОСТ 13219.6–81. Кроме таких корпусов и крышек можно выбрать и другие стандартные корпуса и крышки подшипников ( см. [7] т.2) либо сконструировать крышку самостоятельно (см.[3]). Крышки подбираются по тому же диаметру D, по которому подбирался корпус ( см. Рис.8 ). Однако, крышка должна подходить также по диаметру буртика вала dбп ( см. пункт 2. 3.4 ), а также в нее должно вписываться стандартное манжетное уплотнение
( см. табл.12 ).
Подобрать стандартную крышку, удовлетворяющую всем этим условиям, не всегда удается. В этом случае конструируется нестандартная крышка, основные размеры которой должны совпадать с размерами стандартной. Для подшипникового узла, расположенного в точке 2 (рис.1), необходимы крышки торцовые с манжетными уплотнениями из ГОСТ 13219.5-81 (рис.9, таб. 9) или ГОСТ 13219.6-81 (рис.10, таб.10). А для подшипникового узла, расположенного в точке 5, одна из крышек принимается такой же, как для узла в точке 2, вторая крышка принимается торцовая глухая из ГОСТ 13219.1-81 или из ГОСТ 13219.2-81 (рис.11, таб.11).
Уплотнения предназначены для защиты подшипников от попадания в них пыли, грязи и влаги, а также для предохранения от вытекания смазки. Эти уплотнения могут быть разных конструкций, однако, наиболее предпочтительными являются стандартные манжеты резиновые армированные для валов по ГОСТ 8752-79 (см. таблицу 12). Манжета состоит из корпуса, выполненного из маслобензостойкой резины. Корпус армирован каркасом, представляющим собою стальное кольцо Г-образного сечения. Браслетная пружина стягивает уплотняющую часть манжеты, вследствие чего она плотно охватывает поверхность вала. Манжеты, предназначенные для работы в засоренной среде, выполняют с дополнительной рабочей кромкой, которая называется пыльником.
Номинальный диаметр вала в местах постановки таких уплотнений должен быть равен внутреннему диаметру уплотнения. Участки вала в этих местах должны быть прошлифованы и отполированы, чтобы избежать интенсивного износа уплотнений.
Рис. 9. Крышки торцовые с манжетным уплотнением диаметром до 100 мм, (из ГОСТ 13219.5-81)
Таблица 9. Крышки торцовые с манжетным уплотнением диаметром до 100 мм, (из ГОСТ 13219.5-81), мм
Обозначение крышки | МН 80*45 | МН 80*50 | МН 90*50 | МН100*55 | МН100*65 |
D | |||||
dвала | |||||
d | |||||
D1 | |||||
D2 | |||||
d1 | |||||
d2 | |||||
B | |||||
b | 13,6 | 13,6 | |||
H | |||||
h | |||||
h1 | |||||
h2 | |||||
r | |||||
r1 | 12,5 | 12,5 |
Пример условного обозначения низкой торцовой крышки с манжетным уплотнением диаметром D = 80 мм, dвала = 45 мм: Крышка МН 80*45 ГОСТ 13219.5-81
Рис. 10. Крышки торцовые с манжетным уплотнением диаметром свыше 100 мм, (из ГОСТ 13219.6-81)
Таблица 10. Крышки торцовые с манжетным уплотнением диаметром свыше 100 мм, (из ГОСТ 13219.5-81), мм
Обозначение крышки | МН 110*60 | МН 110*75 | МН 120*65 | МН 120*80 | МН 130*75 | МН 140*80 | МН 140*95 | МН 150*85 | МН 150*100 |
D | |||||||||
dвала | |||||||||
d | |||||||||
D1 | |||||||||
D2 | |||||||||
D3 | |||||||||
D4 | |||||||||
d1 | |||||||||
d2 | |||||||||
n | |||||||||
b | 16,6 | ||||||||
H | |||||||||
h | |||||||||
h1 | |||||||||
h2 | |||||||||
l | |||||||||
s |
Для D = 110 - 150 мм Для D = 80 – 100 мм
Рис. 11. Крышки торцовые глухие низкие ( из ГОСТ 13219.1-81 и ГОСТ 13219.2-81 )
Таблица 11. Крышки торцовые глухие низкие ( из ГОСТ 13219.1-81 и ГОСТ 13219.2-81 ), мм
Обозна-чение крышки | ГН 80 | ГН 85 | ГН 90 | ГН 100 | ГН 110 | ГН 120 | ГН 125 | ГН 130 | ГН 140 | ГН 150 |
D | ||||||||||
D1 | ||||||||||
D2 | ||||||||||
D3 | - | - | - | - | ||||||
B | - | - | - | - | - | - | ||||
d | ||||||||||
d1 | ||||||||||
n | ||||||||||
H | ||||||||||
h | ||||||||||
h1 | ||||||||||
h2 | ||||||||||
l | ||||||||||
s | ||||||||||
r | - | - | - | - | - | - | ||||
r1 | - | - | - | - | - | - |
Для крепления крышек к корпусу подшипника применяется стандартный крепеж, который состоит из болтов, шайб и гаек (см. ниже).
d | S | D | H | l | lo | d | S | D | H | l | lo |
8 - 90 | lo= l при l ![]() ![]() | 23,9 | 20-300 | lo= l при l ![]() ![]() | |||||||
13,1 | 8 - 100 | lo= l при l ![]() ![]() | 26,8 | 20-300 | lo= l при l ![]() ![]() | ||||||
15,3 | 10-150 | lo= l при l ![]() ![]() | 29,6 | 25-300 | lo= l при l ![]() ![]() | ||||||
18,7 | 14-260 | lo= l при l ![]() ![]() | 33,6 | 30-300 | lo= l при l ![]() ![]() | ||||||
21,1 | 16-260 | lo= l при l ![]() ![]() | 35,0 | 35-300 | lo= l при l ![]() ![]() |
Примечание: Размер l (мм) в указанных пределах брать из ряда чисел: 8, 10, 12, 16, 20, 25, 30,
35, 40, 45, 50, 55, 60, 65, 70, 75, 80, 85, 90, 100, 110, 120, 130, 140, 150, 160, 170, 180, 190, 200, 220, 240, 260, 280, 300.
Пример условного обозначения болта диаметром резьбы d = 12 мм, длиной l = 60 мм, с
крупным шагом резьбы, и полем допуска 6g, класса прочности 5.8, с цинковым покрытием толщиной 6 мкм, хроматированным: «Болт М12 – 6g х 60.58.016 ГОСТ 7796 – 70».
Гайки шестигранные с уменьшенным размером под ключ.
ГОСТ 15521 – 70, мм.
d | (14) | (18) | (22) | |||||||
S | ||||||||||
D | 10,9 | 13,1 | 15,3 | 18,7 | 21,1 | 23,9 | 26,8 | 29,6 | 33.6 | |
H | 6,5 | 14,5 |
Пример условного обозначения гайки с диаметром резьбы 12мм, крупным шагом и полем допуска резьбы 6Н, класса прочности 5: «Гайка М12 – 6Н.5 ГОСТ 15521 – 70».
Шайбы пружинные ГОСТ 6402 – 70, мм
Номинальный диаметр резьбы болта, мм | d | S = b | Номинальный диаметр резьбы болта, мм | d | S = b |
6,1 | 14,2 | ||||
8,2 | 16,3 | 3,5 | |||
10,2 | 18,5 | 4,0 | |||
12,2 | 20,5 | 4,5 |
Пример условного обозначения пружинной шайбы для болта с резьбой, диаметра
d = 12мм из стали 65Г: «Шайба 12 65Г ГОСТ 6402 – 70».
Винты установочные с прямым шлицем классов точности А и В
Общие размеры | Рис.1 | Рис.2 | ||||||
d | b | h | c | l1 | l | d1 | l1 | l |
0,8 | 1,8 | 1,0 | - | 5 – 25 | 3,5 | 2,5 | 8 – 25 | |
1,0 | 2,0 | 1,0 | 2,5 | 6 – 30 | 4,5 | 3,0 | 8 – 35 | |
1,2 | 2,5 | 1,6 | 3,0 | 8 – 40 | 6,0 | 4,0 | 10 - 40 | |
1,6 | 3,0 | 1,6 | 4,0 | 10 - 50 | 7,5 | 4,5 | 12 –50 | |
2,0 | 3,5 | 1,6 | 5,0 | 12 - 50 | 9,0 | 6,0 | 16 - 50 |
Таблица 12 - Манжеты резиновые армированные для валов (ГОСТ 8752-79)
| |||||||||||||||||||||||||||||
Группа резины | Рабочая среда | Темература, оС | Окружная скорость, м/с, не более | ||||||||||||||||||||||||||
Минеральные масла, не содержащие серу | -45...+120 | ||||||||||||||||||||||||||||
Вода | +4...+100 | ||||||||||||||||||||||||||||
Минеральные масла с присадками, вызывающими набухание резин группы 1 | -30...+120 | ||||||||||||||||||||||||||||
Масла для гипоидных передач | -30...+100 | ||||||||||||||||||||||||||||
Вода | +4...+100 | ||||||||||||||||||||||||||||
Минеральные масла, не содержащие серу | -30...+120 | ||||||||||||||||||||||||||||
Вода | +4...+100 | ||||||||||||||||||||||||||||
Минеральные масла всех типов. Дизельное топливо | -45...+150 | ||||||||||||||||||||||||||||
РАЗМЕРЫ, мм | |||||||||||||||||||||||||||||
d | D | h1 | h2 | d | D | h1 | h2 | d | D | h1 | h2 | ||||||||||||||||||
Конструирование барабана.
Конструкция барабанов (см. [3]) подобна конструкции шкивов плоскоременных передач. Поэтому для них остаются справедливыми все рекомендации по соотношению размеров, выбору материалов и прочие изложенные в этой литературе.
Барабан отличается от шкива большей шириной (обычно B>D) (см.Рис.12,а), и это вносит некоторые особенности в его конструкцию.
Барабан изготовляют с двумя ступицами и двумя дисками (рис. 12, а и др.) или с одной удлиненной ступицей (рис. 12, б) Последняя конструкция технологичнее, но целесообразна только при сравнительно нешироких барабанах (В < D).
Размеры толщин стенки, ступиц и обода барабана представлены на рис.14 и определяются по эмпирическим зависимостям:
Dст ≥ 1.6d (5)
где d – диаметр вала под ступицу: Dcn - наружный диаметр ступицы,
δо =0.02(Dб + В) (6)
где Dб – диаметр барабана,мм; В – ширина барабана,мм.
Рис.14
δ ≈ (0.9…0.8) δо (7)
δ1 = (Dст – d)/2 (8)
если δ1 / δ >2 то δ2 = 1.5 δ, и h ≥ 4(δ2 - δ) (9)
если δ1 / δ ≤ 2 то δ2 = δ , (10)
и наклонный участок высотой h не делают, а переход оформляется радиусом:
R ≈ 0.5δ. (11)
Большая внутренняя полость (см. рис. 12, а) затрудняет отливку барабана. Во многих случаях (в зависимости от масштаба и возможностей производства) здесь может оказаться целесообразной сварная конструкция.
Конструкция сварного барабана по рис. 13,а аналогична литому по рис. 12, а. Сварная конструкция позволяет снизить толщины элементов и в связи с этим уменьшить вес и расход металла.
Толщины элементов: δо, δ, δ1, определяются по тем же зависимостям, что и для литого барабана (см. выше),а затем их величина уменьшается умножением на коэффициент К = 0,8. ( δ2 = δ ).
Обод сваривают из вальцованного листа или изготовляют из труб. Применение трубы значительно упрощает технологию и целесообразно во всех случаях, когда размеры обода согласуются с размерами стандартной трубы (см. [7]). При выборе трубы необходимо учесть припуск на обработку обода по наружному диаметру.
Обод из листа имеет один или два продольных шва (см. рис. 13,а). Внутреннюю поверхность обода не обрабатывают (см. рис. 13, а и б) или протачивают в местах установки дисков (см. рис. 13, в). Проточка устраняет некруглость или другие дефекты обода, сваренного из листа. Операция проточки сравнительно сложна и трудоемка. Ее можно избежать, если выполнить окружность сварного обода достаточно точной, а диски поставить с зазором (около З - 5 мм), который потом заваривают. На сборочном чертеже зазор можно не показывать, его учитывают в рабочих чертежах. Для обода из труб проточка не требуется, а зазор по дискам может быть не более 1-2 мм. Последовательность операций сварки барабана может быть, например, такой. К ступицам барабана по рис. 14.9, а приваривают диски и ребра; закрепляют ступицы на валу; надевают завальцованный обод, стягивают его на дисках и заваривают продольные швы; сваривают обод с дисками (возможен только один наружный шов) и ребрами; устанавливают барабан на станок по центрам вала и обрабатывают наружную поверхность барабана.
На основе изложенного не трудно установить последовательность операций для барабанов по рис. 13, б и в. Барабан по рис. 13,б не имеет ступиц, шпоночных соединений и пр. Эту простую конструкцию можно считать предпочтительной, однако менее ремонтопригодной. Кроме того при сварке такого барабана возможно коробление вала. Поэтому вал подается на сварку с припусками на последующую обработку шеек. Шейки обрабатывают совместно с наружной поверхностью обода.
Барабан по рис. 13 в, не имеет целого вала. Здесь преследуют цель еще большей экономии материала. Однако изготовление барабана усложняется; трудно точно установить концы валов перед сваркой, возможен значительный увод концов после сварки. С этих позиций здесь целесообразна проточка концов барабана под посадку дисков и увеличенные припуски на обработку шеек вала. Расстояние между дисками рекомендуют принимать (0,6-0,5) В. При этом получают более равномерное распределение нагрузки от ленты по длине барабана. Для удобства сварки или литья иногда допускают отклонения от этой рекомендации и устанавливают диски ближе к краям барабана.
Для фиксирования положения ленты на концах барабана иногда образуют небольшую конусность (см. рис.14). Так как транспортеры имеют малую скорость, а лента дополнительно направляется поддерживающими роликами, выполнение конусов на барабане не обязательно.
В конструкции барабанов с двумя ступицами (см. рис. 12 и 13, а) на валу устанавливают только одну шпонку на ступицу со стороны подвода крутящего момента. В случае установки второй шпонки она будет воспринимать незначительную часть нагрузки, поэтому ее установка считается не целесообразной.
В Приложении показан пример конструкция сварного барабана.
Выбор муфт.
Муфты сужат для соединения валов и перелачи крутящего момента с одного вала на другой. Существует большое количество механических муфт. Однако в нашем случае соединения выходного конца вала редуктора и приводного вала конвейера применяются компенсирующие муфты с жесткими элементами,
а именно цепная или зубчатая (см. [2,3]).
Зубчатая муфта способна компенсировать любые погрешности в соосности валов в достаточно большом диапазоне и обладает большой нагрузочной способностью. Благодаря зубчатому соединению зазоры между зубьями, а значит и люфт не велики, поэтому такую муфту применяют в высоконагруженных реверсивных механизмах. Цепная муфта является упрощенной конструкцией зубчатой муфты. Цепная муфта допускает большие, чем зубчатая погрешности монтажа валов, более проста в эксплуатации и обслуживании. Однако обладает большими зазорами в соединении полумуфт и применяется, как правило, в нереверсивных механизмах.
Выбор стандартных муфтпроизводится по двум основным параметрам:
1. Расчетному крутящему моменту на валу – Тр, Нм.
2. Диаметрам концов соединяемых валов – dк, мм.
Сначала определям Тр по формуле
Тр = kp Т
где kр — расчетный коэффициент, учитывающий динамические нагрузки в условиях эксплуатации; средние значения kр приведены в табл. 13.
Т – номинальный крутящий момент,Нм.(см. МУ п.1, завис.(5)).
далее обращаемся к ГОСТу на выбранный тип муфты (Рис.15 или Рис.16).
Таблица 13. Значения коэффициента kр учитывающего