Литейные напряжения и деформации в отливках
По предложению И.И. Новикова интервал кристаллизации можно разбить на две зоны: жидко-твердую и твердожидкую. В жидко-твердой зоне (при Ту<Т≤Тл, где Ту – температурная граница зон) сплав сохраняет текучесть. При Тс≤T≤Ту в твердожидкой зоне в сплаве содержится количество твердой фазы, необходимое для образования каркаса, проявляющего свойство твердого тела сохранять ранее приданную ему конфигурацию. А.А. Бочвар назвал этот интервал эффективным интервалом кристаллизации сплава (ЭИК). В пределах ЭИК кристаллы образуют остов отливки, но частично отделены друг от друга прослойками расплава. Так как при температуре Т<Ту сплав теряет текучесть, то, начиная с Т=Ту, в отливке будет происходить линейная усадка. При Т>Ту реализуется только объемная усадка.
Рис. 2.6. Схема формы для получения отливки «Крышка» |
Если свободную линейную усадку затормозить, то в отливке возникнут растягивающие деформации. На рис. 4.6 показана схема формы для изготовления отливки «Крышка».
При температуре Т=Ту размер отливки l равен размеру полости формы lo. Если участок полости формы абсолютно податлив, то при охлаждении отливки до температуры Т ее длина будет равна l=lo (1–αт (Ty –T)). При этом никаких напряжений в отливке не возникает. Если форма абсолютно не податлива, то отливка сохранит размер lo, т.е. ее длина будет больше того значения, которое она должна иметь при температуре Т, на величину ∆l=lo–l=lo·αт(Ty–T). Отливка получит относительную деформацию растяжения εу=αт(Ty–T). При этом напряжения равны σр=Е (Т) εу, где Е(Т) – модуль упругости материала при данной температуре.
В общем случае ε=εу−εn+εp, где εn – относительная деформация формы за время усадки; ε – относительная деформация формы вследствие ее теплового расширения при нагреве.
С уменьшением температуры εу увеличивается, достигая при Т=Тс наибольшего значения εmax=αт(Ту–Тс), если пренебречь величинами εn и εp.
Если деформация отливки ε превзойдет деформационную способность сплава ε0, в отливке возникнет горячая трещина. Таким образом, для образования горячей трещины необходимо соблюдение условия εу–εn+εp>ε0.
Из этого неравенства вытекают следующие пути борьбы с горячими трещинами:
1) Улучшение податливости форм, т. е. увеличение εn;
2) Совершенствование конструкции отливки с целью исключения торможения линейной усадки;
3) Синтез сплавов, обладающих низкой горячеломкостью. Горячеломкость – это литейное свойство сплава, определяемое его деформационной способностью ε0 и относительной линейной усадкой εл.
Для оценки горячеломкости, т.е. склонности сплава к образованию горячих трещин, применяют различные технологические пробы. Наиболее ценную информацию дают пробы А. Татюра и Н. Прохорова. В них горячеломкость характеризуется значениями длины отливки Lo, испытывающей торможение усадки, начиная с которых в ней образуются трещины. Чем больше эта длина, тем меньше горячеломкость.
Однако для развития количественной теории образования горячих трещин важно проведение системных исследований деформационной способности сплавов в ЭИК.
Как показали исследования Т.Ф. Баландина и Л.П. Каширцева, деформационная способность сплавов в ЭИК в основном определяется упругой деформацией. Пластическая деформация вблизи температуры солидуса мала. Сравнение деформационной способности сплавов ε0 с относительной свободной усадкой εу позволило установить, что во всем интервале температур ε0>>εу.
В исследованиях Г.Ф. Баландина и Л.П. Каширцева показано, что реологическое поведение сплавов адекватно описывается моделью тела Шведова (см. рис 1.9). Тело Шведова состоит из последовательно соединенных тел Гука, Бингама и Кельвина. Параметры тела Гука определяют упругую деформацию тела, тела Бингама – пластическую, а параметры тела Кельвина – деформацию упругого последействия. Тело характеризуется пятью параметрами: модулем упругости Е1 тела Гука, модулем упругости Е2, определяющим упругое последействие, пластической вязкостью тела Бингама η1, псевдовязкостью тела Кельвина η2 и предельным касательным напряжением σs. К сожалению, экспериментальные данные по этим параметрам для сплавов очень ограничены. Практически весь комплекс параметров получен Г.Ф. Баландиным и Л.П. Каширцевым только для ряда сплавов системы Al–Si.
Механическое поведение тела Шведова при напряжениях, меньших предельного касательного напряжения, описывается следующим дифференциальным уравнением:
· При σ≤σs
, (2.16)
где VD=const – постоянная скорость относительной деформации тела, с-1.
Начальное условие для данного уравнения: при t=0 τ=0, dσ/dt=VD·E1, где t0 – время достижения напряжением значения σ=σs.
· При σ>σs
(2.17)
Начальное условие: при t=t0 σ=σs, dσ/dt=VD·E1. Для того чтобы рассчитать деформационную способность сплава при температуре Т в интервале Ту≤Т≤Тс, необходимо выполнить решение уравнений (2.16) и (2.17) при разных температурах при последовательном наращивании времени. Требуется определить время, в течение которого напряжение достигает значения предела прочности сплава при данной температуре σпр. В процессе решения выполняется расчет упругой деформации εупр, пластической деформации εпл, деформации упругого последействия εnд, а также полной деформации εу=εупр+εпл+εnд. Так как этот расчет очень трудоемкий, то для его выполнения разработана программа, приведенная в прил. 2.
Как показали эксперименты, деформация упругого последействия мала, и ею можно пренебречь. С учетом этого уравнения (4.16) и (4.17) упрощаются и можно получить следующие простые расчетные формулы:
· При σ≤σs σ=VD·E1t; t0=σs/(VD·E1); εпл=0; εнд=0; εупр=0; δ=σ/E1.
При t=t0 ε=σ/E1.
· При σ>σs σ=σs+VD·E1(t–t0); время нагружения до разрыва образца tk=t0+(σпр–σs)/VD·E1; ; εупр=σпр/E1; εпд=0; ε=εупр+εпл. Как показали расчеты и эксперименты, εупр>>εпл.
Пример1. Выполним расчет деформации алюминиево-кремнистого сплава (0,6% Si) по приведенной выше методике.
При температуре 640 оС Е1=9 МПа, Е2=3,8 МПа, η1=6000 МПа·с, η2=250 МПа·с, σs=0,00125 МПа, σпр=0,15 МПа. Скорость деформации VD=0,00015 с-1, αт=0,000024 к-1.
t0= с; E=Eупр=
%.
При t=tk=0,9+ c Eупр=
%.
Eпл= %. Eд=Eупр+Eпл=1,80 %.
Eу=0,000024 %. Видно, что Eд>>Eу.
Причина образования горячих трещин связана с неравномерным развитием деформации εу в различных частях отливки. В реальной отливке различные ее части охлаждаются с разной скоростью, имеют разные температуры и различные реологические и прочностные характеристики. В элементах отливки, которые охлаждаются медленнее, меньше значение модуля упругости. Поэтому усадочные процессы будут преимущественно локализоваться в этих элементах. Относительная усадка в них ε=mεy, где m>1 – коэффициент, учитывающий неравномерность охлаждения отливки. В этом случае, если m εy>ε0, в отливках образуется горячая трещина.
На рис. 4.7 приведена схема неоднородно затвердевающих отливок. На рис. 4.7, а отливка имеет местное утолщение, а на рис. 4.7, б затвердевание центральной части замедляется применением малотеплопроводного покрытия в металлической форме.
Рис. 2.7. Схема неоднородно затвердевающих отливок: а – отливка имеет местное утолщение; б – охлаждение центральной части отливки замедлено |
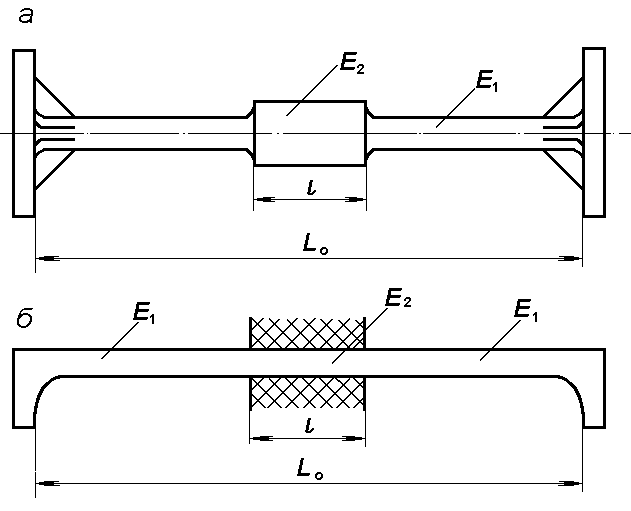
Для расчета относительной деформации ε центральной, замедлено охлаждающейся части отливки в момент, когда температуры частей отливки равны Т1<Ту (для быстро охлаждающейся части) и Т2<Ту (для медленно охлаждающейся части), где Т2>Т1, можно получить следующую формулу:
, (2.18)
где Е2 – модуль упругости сплава при Т=Т2;
Е1 – модуль упругости сплава при Т=Т1.
Так как Т2>Т1, то Е2<Е1. Формулу (4.16) можно записать в виде
ε2=mεy2, (2.19)
где
Величина m растет с увеличением отношения L0/l и разности температур (Т2–Т1), которая увеличивается с ростом перепада толщин стенок отливки.
Горячая трещина образуется, когда выполняется условие Е2mεy2≥σB, где σB – предел прочности сплава при заданной температуре.
Для нахождения коэффициента m в реальных условиях необходимо решить комплексную задачу – тепловую по расчету температурного поля отливки и задачу, совмещенную с реологическими уравнениями для расчета деформации сплава. При этом необходимы данные по реологическим и прочностным характеристикам сплава в зависимости от температуры. К сожалению, в настоящее время системные данные по этим характеристикам отсутствуют.
На основании имеющихся в литературе данных для среднеуглеродистой стали в температурном интервале ЭИК можно написать следующие формулы для температурной зависимости предела прочности σВ и модуля упругости Е:
Е=15500–10Т; (2.20)
σВ=50–Т/30, (2.21)
где Е – модуль упругости стали, МПа;
σВ – предел прочности стали, МПа.
Для выполнения приближенных расчетов по формуле (2.18) расчет изменения температуры элементов отливки, изображенной на рис. 2.7, выполним по методу Г.Ф. Баландина.
, (2.22)
, (2.23)
где bф – коэффициент аккумуляции тепла материалом формы, Вт·с1/2/(см2·К);
Т0– начальная температура формы, оС;
R1 и R2– приведенные толщины стенок элементов отливки, см;
, Дж/(г·К);
ρж-m – плотность сплава в интервале ЭИК, г/см3.
(2.24)
(2.25)
Подставив выражения (2.20) и (2.21) для (Ту–Т1) и (Ту–Т2) в уравнение (2.16), получим формулу, описывающую изменения относительной деформации в массовом узле отливки со временем t.
Условие образования трещины имеет вид
(15500–10Т2)·ε2>(50–Т2/30). (2.26)
Здесь ε2 – выражение (2.18) с учетом (2.22) и (2.23). В правую часть неравенства (2.26) подставлено выражение для Т2, полученное из (2.21). В (2.26) искомой переменной является время t, которое следует варьировать от времени достижения температуры Т=Ту массивной частью отливки, определенного по формуле (2.25), до времени достижения температуры солидуса массивной частью отливки, равного
.
Если неравенство (2.26) в этом интервале не выполняется, то образование горячей трещины не произойдет.
Неравенство неразрешимо алгебраически относительно времени t. Поэтому для его решения следует применить численные методы. В прил. 2 приведена программа, написанная на языке Borland Pascal, позволяющая на основе численного решения неравенства (2.26) определить, образуется ли горячая трещина при заданных условиях.
В качестве определяющих факторов необходимо принять отношение L0/e, отношение R2/R1 и значение коэффициента аккумуляции тепла формой bф. Как показывают выполненные расчеты, при малых отношениях L0/e и R2/R1 трещины не образуются. Однако при некотором значении происходит образование трещины.
При пользовании программой необходимо по запросам компьютера задать значения R1, R2, L0, е в см и bф в Вт·с1/2/(см2·К). В результате выполнения расчетов на печать выводится сообщение о наличии или отсутствии трещины, данные о напряжении в массивной части отливки и ее относительной деформации, а также значение коэффициента m в уравнении (2.19).
Пример 2. Рассмотрим результаты расчетов при R1=2 см, R2=5см, е=8 см и bф=0,15 Вт с1/2/(см2·К).
При L=15 см трещина не образуется, m=3,0, относительная деформация массивной части ε2=0,15% при εу=0,05 %.
При L=16 см трещина не образуется, m=3,2, ε2=0,16 % при εу=0,05 %.
При L≥18 см происходит образование трещины, т.е. (L/e)=2,25. При L=18 m=3,6, ε2=0,17 % при εу=0,05 %.
В процессе охлаждения отливки ниже температуры солидуса в ней возникают напряжения, вызванные механическим и термическим торможением усадки. Механическое торможение усадки стержнями и участками формы приводит к образованию усадочных напряжений. Считается, что усадочные напряжения временные, так как после выбивки отливки они снимаются. Однако, если во время выбивки или удаления отливки из формы температура ее отдельных узлов различна, после выбивки остаточные напряжения в отливке сохраняются. Если два жестко связанных элемента отливки имеют в момент выбивки разные температуры Т1<Т2, то остаточные напряжения можно оценить по формулам
(2.27)
где S1и S2 – площади сечений первого и второго узлов отливки.
В тонких частях отливки действуют растягивающие напряжения, а в толстых – сжимающие. Термическое торможение усадки возникает вследствие неравномерного ее развития в различных элементах отливки.
Механическое поведение расплава в рассматриваемом интервале температур (при охлаждении отливки) отличается от рассмотренного выше (в интервале Тл – Тс) тем, что интервал температур при этом значительно шире. Начиная с температуры солидуса, резко увеличивается пластичность сплава, которая при дальнейшем понижении температуры сплава уменьшается. Вблизи температуры солидуса превалирует пластическая деформация и деформация упругого последействия. При снижении температуры увеличивается упругая деформация. При температуре ниже некоторой величины Тп сплав можно считать пластичным телом, в котором не развиваются напряжения. При Т<Тп сплав ведет себя как упругое тело, подчиняющееся закону Гука.
Термические напряжения определяются перепадами температур тонкой, быстро охлаждающейся и толстой частей отливки в момент перехода температуры толстой части через значение Т=Тп. Принимают, что Тп=(0,4÷0,5) Тс. Для чугуна и стали Тп=400÷500 оС.
Термические напряжения остаточные. Они возникают не только в отдельных элементах отливки, регулирующихся толщинами стенок, но и по сечению отливки. При этом в наружных быстро охлаждающихся зонах отливки или тонких элементах отливки возникают сжимающие напряжения, а в центральных слоях или толстых элементах – растягивающие.
Для оценки термических напряжений в жестко связанных тонких и толстых элементах отливки, охлаждающейся в песчаной форме, можно применить следующие формулы:
; (2.28)
, (2.29)
где Тп – температура перехода сплава из пластического состояния в упругое;
Т1 – температура тонкого элемента отливки в момент перехода толстого элемента из пластического состояния в упругое.
Для определения разности температур (Тп–Т1) нужно рассчитать кинетику охлаждения отливки после достижения температуры Т=Тс. Для расчета охлаждения плоской отливки можно применить формулу
(2.30)
Применяя формулу (2.30) для тонкого и толстого элементов отливки, получим следующее выражение для расчета величины (Тп–Т1):
(2.31)
где R1 и R2– приведенные толщины стенок тонкого и толстого элементов отливки;
Т0– начальная температура формы;
bф1 и bф2 – коэффициенты аккумуляции тепла формой около тонкого и толстого элементов.
Из уравнения (2.31) видно, что перепад температур (Тп–Т1), а следовательно, и напряжения зависят от отношения . При
=1 напряжения равны нулю. Для того чтобы снизить напряжения, нужно уменьшить отношение
. При заданных значениях R1 и R2 для этого необходимо увеличить коэффициент аккумуляции тепла bф2 около массивного элемента (например, применить более теплопроводную смесь или наружный холодильник). Рассмотрим в качестве примера решение следующей задачи.
Пример 3. Определить уровень напряжений в отливке, имеющей в конструкции два связанных друг с другом стержня при R1=1 см; R2=3 см; S1=30 см2; S2=90 см2. Установить, образуется или нет холодная трещина. В случае образования трещины определить значение bф2 для ее устранения.
Материал отливки – среднеуглеродистая сталь. Тзал=1600 оС; Тл=1497 оС; Тс=1447 оС; ρт=7,5 г/см3; ρж=7 г/см3; ρж-т=7,25 г/см3; предел прочности стали σВ=500 МПа; сж=0,69 Дж/(г·К); сж-т=0,76+258/50= =5,9 Дж/(г·К); ст=0,84 Дж/(г·К); Тп=500 оС; Т0=20 оС; bф1=0,15 Вт с1/2/(см2·К); bф2=0,3 Вт с1/2/(см2·К).
По формуле (2.31) находим
оС.
σ1= МПа;
σ2= МПа.
Так как σ1>σВ=500 МПа, то в отливке возникает холодная трещина. Необходимое для устранения холодной трещины значение bф2 можно найти, разрешив относительно уравнение (2.31), приняв
оС.
Из уравнения (2.31) находим
(2.32)
Подставив в уравнение (2.32) значение известных величин, получим 1,39. Отсюда находим, что для устранения трещины нужнопринять
Вт·с1/2/(см2·К).
Более детально вопросы термических напряжений рассматриваются в курсах термопластичности и термоупругости.
Контрольные задания
Рис. 2.8. Сечение отливки |
Задание 2.1.Для отливки, сечение которой приведено на рис. 2.8, определить размеры модели и стержневого ящика с учетом линейной усадки и степени ее торможения. Условия задания приведены в табл. 2.1.
Задание 2.2. Определить объем сплава после охлаждения приведенной на рис. 2.8 отливки до температуры Тк =20 оС, а также объем отливки после ее охлаждения. Сравнить полученные объемы. Степень торможения усадки Кт принять равной 1. Условия расчетов приведены в табл. 2.2.
Указание. Объем полости формы, равный объему жидкого сплава, залитого в нее, следует рассчитать в соответствии с размерами на чертеже (см. рис. 2.8), откорректированными с учетом линейной усадки (εл). Толщину отливки в направлении, перпендикулярном чертежу, принять равной 1 мм. Объем отливки нужно рассчитывать по размерам, указанным на чертеже. Для вычисления объема сплава следует применить формулы (2.1)–(2.4).
Таблица 2.1 - Исходные данные к заданию 2.1
Номер варианта | Сплав | εл, % | Степень расширения по размерам | |||
Серый чугун | 0,8 | 0,9 | ||||
Углеродистая сталь | 0,7 | |||||
Сталь 110Г13Л | 2,8 | 0,7 | ||||
Сплав АК12 | 0,8 | 0,7 | 0,9 | |||
Сплав АК7ч | 1,4 | 0,7 | 0,9 | |||
Белый чугун | 1,7 | 0,8 |
Задание 2.3.Определить объем усадочной раковины в отливке. Насколько изменится объем усадочной раковины: а) при полном торможении линейной усадки; б) при увеличении температуры заливки на 100 оС. Условия задания приведены в табл. 2.3. Расчеты выполнять по формуле (2.5).
Задание 2.4.С помощью метода «вписанных окружностей» определить термические узлы в отливке и проверить соблюдение принципа направленного затвердевания (материал отливки – углеродистая сталь). Для узлов, в которых он не выполняется, построить профиль технологических напусков. Построить чертеж отливки с учетом напусков и указать на нем окончательные размеры. Схемы отливок указаны в табл. 2.4. При построении напусков следует использовать методику, показанную на рис. 2.1, б и 2.2, б. Криволинейный контур необходимо спрямлять, как показано на рис. 2.1, б.
Задание 2.5.Для отливок, схемы которых указаны в табл. 2.4 с откорректированными с учетом напусков размерами, выполнить расчет прибыли по методу Й. Пржибыла. Температуру ликвидуса стали принять равной Тл=1497 оС. Расчет выполнить в соответствии с последовательностью, приведенной выше (с. 30-31). Исходные данные для расчетов приведены в табл. 2.4.
Задание 2.6.Для отливок, схемы которых приведены в табл. 2.4, определить массу внутренних холодильников, которые следует установить в термический узел отливки в месте нарушения принципа направленного затвердевания, чтобы исключить применение технологических напусков. Теплофизические свойства сплава и холодильника принять следующие: L=258 Дж/г, сж=0,92 Вт/г, Ткр=1472 оС, сx=0,75 Дж/г, Тc=1440 оС. Масса узла mт.у=ρ1·V=7,5 Vт.у, где Vт.у – объем термического узла, см3. Расчеты выполнить по формуле (2.7).
Таблица 2.2 - Исходные данные к заданию 2.2
Номер варианта | Сплав | αVж, K-1 | αVт, K-1 | εVз, % | εVр, % | εVy→α, % | Тзал, оС | Тл, оС | Тс, оС | εл, % |
Серый чугун | 2·10-4 | 2.1 10-4 | 2,0 | –1 | –0,5 | 0,8 | ||||
Белый чугун | 2 10-4 | 2.1 10-4 | 2,0 | –0,5 | 0,8 | |||||
Углеродистая сталь | 0,8 10-4 | 5,0 10-4 | 3,0 | –1,0 | 2,1 | |||||
Сталь 110Г13Л | 1,6 10-4 | 6,0 10-4 | 6,0 | 2,7 | ||||||
Сплав АК12 | 1,2 10-4 | 4,2 10-4 | 3,8 | – | 0,8 | |||||
Сплав АК7ч | 1,2 10-4 | 7,1 10-4 | 3,0 | – | 1,4 | |||||
Серый чугун | 2 10-4 | 2,5 10-4 | 2,0 | –1 | –0,5 | – | ||||
Белый чугун | 2 10-4 | 2,5 10-4 | 2,0 | –0,5 | – | |||||
Углеродистая сталь | 0,8 10-4 | 5,0 10-4 | 3,0 | –1,0 | – | |||||
Сталь 110Г13Л | 1,6 10-4 | 6,0 10-4 | 6,0 | – | ||||||
Сплав АК12 | 1, 10-4 | 4,2 10-4 | 3,8 | – | – | |||||
Сплав АК7ч | 1,2 10-4 | 4,2 10-4 | 3,0 | – | – |
Задание 2.7.Рассчитать усадочную пористость в отливке. Исходные данные для расчетов приведены в табл. 2.5. Как изменится пористость, если содержание водорода в сплаве [H] уменьшить в 2 раза, давление p0 увеличить в 1,5 раза, Nз увеличить в 10 раз за счет модифицирования сплава? Расчеты выполнить по приближенной формуле (2.12) при y=H∕2 и y=H. Выполнить также расчеты на компьютере по программе «Пористость», приведенной в прил. 2. Константу затвердевания в расчетах принять равной m=0,15 см∙с–1/2. Выполнить расчеты газовой пористости по формуле (2.15) для алюминиевых сплавов.
Задание 2.8.Вывести уравнения (2.16) и (2.17) для тела Шведова и получить их решения для σ(t). Получить уравнения для расчета деформаций εупр, εпл, εпд и ε.
Указания. Следует ознакомиться с рекомендациями, приведенными в гл. 1. Решение проводить при постоянной скорости деформации тела, т.е.
Принять при σ<σs;
Необходимо повторить тему из курса высшей математике по решению дифференциальных уравнений второй степени с постоянными коэффициентами.
Задание 2.9.Для алюминиево-кремниевого сплава рассчитать для разных температур величины εупр, εпл и ε при σ=σпр, где σпр – предел прочности сплава при данной температуре. Построить графики зависимости деформационной способности сплава εу и ε от температуры в заданном интервале температур. Сравнить εу с εус=αт(Ту–Т).
Расчеты выполнить по рассмотренной выше упрощенной методике и при решении уравнений (2.16) и (2.17) на компьютере с использованием программы «Деформационная способность сплава», приведенной в прил. 2. При расчетах по программе ввести по запросу компьютера номер варианта FF. В задании предусмотрены расчеты для двух сплавов: с содержанием кремния Si=0,6 % и Si=5 % (индекс сплавас содержанием 0,6 % Si F=2, индекс сплавас содержанием 0,6 % Si F=1). Условия расчетов приведены в табл. 2.6, реологические свойства сплавов при разных температурах в табл. 2.7 и 2.8.
Таблица 2.3 - Исходные данные к заданию 2.3
Номер варианта | Сплав | αVж, К–1 | εVз, % | αVт, К–1 | εVр, % | Tзал, оС | Tл, оС | Tс, оС | Vо, см3 |
Углеродистая сталь | 0,8·10–4 | 3,0 | 5,0·10–5 | –1 | |||||
Серый чугун | 2,0·10–4 | 2,0 | 2,1·10–5 | ||||||
Белый чугун | 2,0·10–4 | 2,0 | 2,1·10–5 | ||||||
Сталь 110Г13Л | 1,6·10–4 | 6,0 | 6,0·10–5 | ||||||
Сплав АК12 | 1,2·10–4 | 3,8 | 4,2·10–5 | ||||||
Сплав АК74 | 1,2·10–4 | 3,0 | 7,1·10–5 | ||||||
Серый чугун | 2,0·10–4 | 2,0 | 2,1·10–5 | –1 | |||||
Углеродистая сталь | 0,8·10–4 | 3,0 | 5,0·10–5 | ||||||
Сталь 110Г13Л | 1,6·10–4 | 6,0 | 6,0·10–5 | ||||||
Сплав АК12 | 1,2·10–4 | 3,8 | 4,2·10–5 | ||||||
Сплав АК74 | 1,2·10–4 | 3,0 | 7,1·10–5 | ||||||
Белый чугун | 2,0·10–4 | 2,0 | 2,1·10–5 | ||||||
Серый чугун | 2,0·10–4 | 2,0 | 2,1·10–5 | –1 | |||||
Белый чугун | 2,0·10–4 | 2,0 | 2,1·10–5 | ||||||
Углеродистая сталь | 0,8·10–4 | 3,0 | 5,0·10–5 | ||||||
Сталь 110Г13Л | 1,6·10–4 | 6,0 | 6,0·10–5 | ||||||
Сплав АК12 | 1,2·10–4 | 3,8 | 4,2·10–5 | ||||||
Сплав АК74 | 1,2·10–4 | 3,0 | 7,1·10–5 | ||||||
Углеродистая сталь | 0,8·10–4 | 3,0 | 5,0·10–5 | ||||||
Сталь 110Г13Л | 1,6·10–4 | 6,0 | 6,0·10–5 |
Таблица 2.4 - Исходные данные к заданиям 2.4, 2.5
Номер варианта | Схема отливки (номер рис.) | Vo, см3 | Tзал, оС | β | Д1, см | Д2, см | d, см | Н, см | Н1, см | Н2, см |
2.9 | 0,08 | |||||||||
« | 0,15 | |||||||||
« | 0,17 | 12,5 | ||||||||
« | 0,08 | |||||||||
« | 0,15 | |||||||||
« | 0,17 | |||||||||
« | 0,15 | |||||||||
2.10 | 0,08 | |||||||||
« | 0,15 | |||||||||
« | 0,17 | 12,5 | ||||||||
« | 0,08 | |||||||||
« | 0,15 | |||||||||
« | 0,13 | |||||||||
« | 0,14 | |||||||||
« | 0,15 | 12,5 | ||||||||
2.11 | 0,08 | |||||||||
« | 0,15 | |||||||||
« | 0,17 | 12,5 | ||||||||
« | 0,08 | |||||||||
« | 0,15 | |||||||||
« | 0,17 | |||||||||
« | 0,15 | |||||||||
2.12 | 0,08 | |||||||||
« | 0,15 | |||||||||
« | 0,14 | 12,5 | ||||||||
« | 0,08 | |||||||||
« | 0,15 | |||||||||
« | 0,13 | |||||||||
« | 0,08 |
Таблица 2.5 - Исходные данные к заданию 2.7 | ||||||||||||
Номер варианта | Сплав | εV1Σ, % | Кз | μ, Па·с | Nз, см–3 | α, см2·с–1 | [H], см3 100 г | Кр, см3·Па–1/2 100 г | Н, см | R, см | Vо, см3 | pо, Па |
Сталь 35Л | 0,040 | 0,70 | 5,5·10–3 | 0,0052 | 0,10 | 0,0007 | 1,5 | 0,20 | ||||
АК7ч | 0,045 | 0,15 | 2,0·10–3 | 0,0271 | 0,15 | 0,0025 | 1,5 | 0,17 | ||||
Al–Mg | 0,050 | 0,05 | 2,4·10–3 | 0,1360 | 0,15 | 0,0060 | 1,5 | 0,44 | ||||
Al–Cu |