Назначение, особенности, виды и материалы покрытий, предъявляемые к ним требования
Глава 5. Научные, методологические и производственные проблемы обеспечения работоспособности и ресурса деталей ГТД
Общие сведения
В процессе эксплуатации приповерхностные объемы материала испытывают наибольшие нагрузки, контактируя с сопряженными деталями и потоками частиц, непосредственно взаимодействуя с внешней средой, поэтому структурно-фазовое состояние, химический состав поверхностного слоя и его микрогеометрия определяют работоспособность и ресурс многих ответственных деталей.
Поверхностный слой, толщина которого находится в пределах от десятков ангстрем до десятых долей миллиметра, характеризуется структурой и свойствами, отличными от основного материала. Это обусловлено тремя основными причинами:
- особым состоянием атомов на поверхности (наличие свободных связей) и как следствие свободной поверхностной энергией и большой адсорбционной активностью;
- измененными в результате технологического воздействия структурой, фазовым и химическим составом;
- повторными механическими, тепловыми и физико-химическими воздействиями в процессе эксплуатации.
Несущая способность поверхностного слоя – комплексное понятие, характеризующее сопротивление поверхности и приповерхностных объемов материала внешним факторам. Например, несущая способность при контактном нагружении зависит от сопротивляемости поверхностного слоя статическим и динамическим воздействиям, усталостным процессам, абразивному разрушению, схватыванию и т.д. Исходными данными для ее оценки являются твердость, шероховатость, толщина упрочненного слоя, уровень и знак остаточных напряжений, свойства материалов сопряженных деталей.
Процессы, протекающие в поверхностном слое при эксплуатации, зависят от его состояния после технологической обработки, условий нагружения, механики и физико-химических особенностей контактного взаимодействия.
Взаимосвязи перечисленных факторов образуют сложную динамическую систему, в которой изменение состояния поверхностного слоя в процессе эксплуатации влечет изменение условий нагружения (рис. 5.1).
В частности, приработка рабочих поверхностей и формирование на них вторичных структур приводят к снижению коэффициента трения, что уменьшает и изменяет характер действующих нагрузок.
Рис. 5.1. Структура динамической системы поверхностный
слой –условия нагружения
Как и любая другая динамическая система, она может находиться в состоянии устойчивого равновесия, когда всякое изменение в поверхностном слое или уровне действующих нагрузок вызывает к действию процессы, приводящие систему в равновесное состояние (замена разрушенных вторичных структур новыми, приработка и залечивание образующихся задиров и др.).
Возможны условия нагружения, при которых равновесное состояние динамической системы невозможно, например не обеспечиваются нормальные условия контактного взаимодействия (задирообразование, интенсивное абразивное разрушение и др.). В этих случаях необходимы дополнительные конструкторские или технологические мероприятия.
Отыскание прямых связей этих параметров с эксплуатационными свойствами - трудоемкий процесс. Тем более что эти параметры часто взаимосвязаны и разделить их влияние сложно, а подчас невозможно. Решение подобных задач усложняется многообразием условий нагружения и процессов, протекающих в поверхностном слое при эксплуатации.
Оптимальные параметры состояния поверхностного слоя определяются условиями нагружения.
Величина и характер действующих нагрузок зависят от конструкции узла, условий его сборки и эксплуатации. В случае когда невозможно или нерационально уменьшение уровня действующих нагрузок с помощью конструкторских приемов (изменение габаритов, конструктивных элементов, материалов), равновесное состояние системы поверхностный слой–условия нагружения обеспечивается способами упрочняющей технологии. Упрочнение целесообразно использовать и в тех случаях, когда требуется увеличить ресурс изделия, повысить надежность или получить какие-либо специальные свойства поверхностей деталей.
Необходимость получения эксплуатационных и специальных свойств поверхностного слоя обусловила возникновение целого направления в технологии, которое за рубежом называют «surface engineering». В нашей стране принято использовать термин «поверхностное упрочнение», который обычно трактуется в широком смысле. При этом имеются в виду свойства поверхностного слоя, часто не связанные с механической прочностью. Например, твердость и прочность не являются критериями, определяющими жаростойкость и сопротивление коррозии поверхностного слоя.
Упрочнение металла в механическом (прочностном) толковании может быть обусловлено разнообразными по физической сущности факторами, причем сами критерии прочности определяются условиями нагружения детали и оцениваются разными характеристиками. В одних случаях это твердость (сопротивление абразивному изнашиванию), в других - предел усталости (динамическое нагружение), в третьих - предел прочности и т.д.
Современное материаловедение выделяет следующие основные направления повышения прочностных свойств материалов:
- деформационное упрочнение (наклеп), происходящее за счет увеличения плотности дислокаций;
- легирование, обеспечивающее упрочнение путем «связывания» дислокаций атомами легирующих элементов;
- фазовые превращения, вызываемые термическим и деформационным воздействиями;
- фазовый наклеп;
-механическое введение в сплав или выделение в нем дисперсных частиц;
- формирование метастабильных (в том числе аморфных) структур при закалке из жидкой фазы.
Следует отметить, что при поверхностном упрочнении имеют место некоторые дополнительные механизмы увеличения прочности, связанные со строением поверхностного слоя и особенностями технологического воздействия на него. Последние приводят к неравномерности нагрева, деформации, концентрации легирующих элементов по глубине и как следствие к возникновению остаточных напряжений первого рода, градиентов твердости и др. Сюда следует отнести и упрочнение за счет физико-химического модифицирования поверхностного слоя, нанесения покрытий, текстурообразования. На прочность поверхностного слоя оказывает влияние соотношение характеристик подложки и упрочняемого слоя, в частности твердостей, коэффициентов термического расширения, электрохимических параметров.
Существующие способы поверхностного упрочнения можно отнести к следующим основным группам:
- упрочнение без изменения химического состава поверхностного слоя;
- поверхностное легирование и физико-химическое модифицирование;
-нанесение покрытий
-комбинированные методы упрочнения.
Упрочнение без изменения химического состава выполняется:
- поверхностным пластическим деформированием (ППД);
- поверхностным закаливанием;
- обработкой холодом.
Поверхностное легирование заключается в создании на поверхности легированного слоя, состав которого обеспечивает требуемые эксплуатационные свойства, а физико-химическое модифицирование - в образовании на поверхности слоя химических соединений материала детали за счет протекания химических реакций или образования метастабильных структур, например аморфных.
На практике используют следующие способы поверхностного легирования и физико-химического модифицирования:
- обработка в плазме (например, азотирование, напыление и др.);
- обработка в электронных лучах (например, легирование поверхности из твердой фазы при нагреве электронным пучком и др.);
- обработка в лазерных лучах (например, лазерное поверхностное твердофазное легирование и др.);
- химико-термическая обработка (например, алитирование, борирование и др.);
- ионная имплантация (например, облучение ионным пучком и др.).
Для защиты деталей авиационной техники от коррозии, износа, эрозии, окисления применяют различные способы нанесения покрытий. Покрытия часто используются также в технологических целях для защиты от насыщения при химико-термической обработке, от брызг металла при сварке, от окисления, для снижения трения при обработке давлением и т.д.
Как было сказано выше, для поверхностного упрочнения применяют отличающиеся по природе упрочняющего воздействия методы: ППД, химико-термическую обработку, высококонцентри-рованные потоки энергии (лазерные, электронно-лучевые, ионные), нанесение покрытий из материалов с высокими эксплуатационными свойствами и др.
В силу тех или иных причин (увеличение шероховатости, снижение усталостной прочности, высокая пористость, недостаточная прочность сцепления покрытия с подложкой и т.д.) сфера использования многих, несомненно, эффективных процессов упрочнения существенно ограничена. В подобных случаях сочетание с другим способом упрочнения (снижающим шероховатость, повышающим усталостную прочность, уменьшающим пористость, увеличивающим прочность сцепления и др.) дает возможность добиться требуемого состояния поверхностного слоя и тем самым обеспечить высокий уровень эксплуатационных свойств, расширить технологические возможности.
Кроме того, комбинированной обработкой решают задачи увеличения маслоемкости поверхностей трения, упрочнения подложки под наносимое покрытие, повышения точности и т.д.
Методы комбинированного упрочнения целесообразно применять для наиболее ответственных деталей в случаях, когда традиционная технология не обеспечивает требуемый уровень эксплуатационных свойств.
Многообразие упрочняющих эффектов и способов упрочнения представляет широкие возможности по их комбинированию.
Назначение, особенности, виды и материалы покрытий, предъявляемые к ним требования
Около 75 % деталей авиационных двигателей имеет металлические или керамические покрытия для защиты от коррозии, износа и высокотемпературного окисления, а также для специальных целей, например уплотнения. Типичный пример многослойного покрытия приведен на рис. 5.2.
Выбор материала и способа нанесения покрытия производится с учетом следующих основных положений.
1. Условия эксплуатации покрываемой детали или узла (температура,
условия контакта, среда и др.).
2. Химическая и металлургическая совместимость материалов покрытия и подложки, которая предполагает образование прочных связей между ними и отсутствие электрохимического взаимодействия. При этом следует учитывать возможность уменьшения прочности сцепления покрытия с подложкой в процессе эксплуатации в связи с возможным выделением на их границе фаз, образованием хрупких соединений, коррозионными процессами и проч.
3. Возможность нанесения покрытия на данный материал выбранным
способом.
4. Физико-механическая совместимость. Подразумевает близость физических и механических свойств материалов покрытия и подложки, в частности модулей упругости, твердости, коэффициента термического расширения.
Рис. 5.2. Пример микроструктуры многослойного покрытия (в сечении)
5. Возможность получения структуры покрытия с заданным комплексом свойств.
6. Возможность нанесения покрытия на деталь данной формы с обеспечением равномерности толщины и свойств.
Общая информация по покрытиям приведена в прил. 5 (см. стр. 662).
Уплотнительные покрытия. Уменьшая величину зазоров между лопатками и кожухом (между ротором и статором)можно повысить эффективность двигателя на 5 %. Этого можно добиться, например, нанесением на внутреннюю поверхность деталей статора срабатываемых (уплотнительных) покрытий, которые, изнашиваясь при взаимодействии с лопатками вращающегося ротора, формируют минимальный зазор (рис. 5.3). Места нанесения уплотнительных покрытий показаны на рис. 5.4.
![]() |
Рис. 5.3. Использование срабатываемого покрытия для минимизации зазора между торцом лопатки и элементами статора двигателя
Срабатываемые покрытия должны иметь малое сопротивление изнашиванию при сравнительно высокой прочности и жаростойкости. Эффективная величина зазора должна сохраняться в течение ресурса работы двигателя. Этот комплекс свойств обеспечивается специфическим строением многокомпонентных материалов, свойствами используемых связок, пористостью, технологией нанесения покрытий. Рекомендуется использовать в качестве срабатываемых материалов полимеры, кремнеорганические полимеры с алюминиевым наполнителем, композиции Ме-полимер-нитрид бора, металлографитовые композиции (Ni-25 % С), покрытия Me-Cr; Al; Y, окись циркония, стабилизированную иттрием. Тот или иной материал назначается в зависимости от действующих температур (рис. 5.5). При температурах, превышающих 800 °С, рекомендуются керамические термобарьерные покрытия (ZrO2-Y2O3).
![]() |
Рис. 5.4. Места нанесения уплотнительных покрытий
Рис. 5.5. Материалы, применяемые для изготовления лопаток и нанесения уплотнительных покрытий:
а – композиционные полимерные материалы; б – титановые сплавы; в – стали; г – сплавы на никелевой и кобальтовой основах; д – сплавы с направленной кристаллизацией; е – сплавы с монокристаллической структурой; ж – оксидно-дисперсно-упрочненные сплавы;
1- полимеры; 2 – полимеры с наполнителем из алюминиево-кремниевых сплавов или Al-BN; 3 – композиция металл-твердая смазка (Ni-25%С); 4 – пористые композиции Me, Cr, Al, Y; 5 – керамические материалы (ZrO2-Y2O2)
В двигателе АЛ-31 в качестве срабатываемых покрытий, работающих до температур порядка 550 °С, используется материал АНБ, исходные гранулы которого содержат 18 ... 23 % BN, 4 ... 8 % SiО2, остальное - алюминий. При более высоких температурах применяются пористые и керамические материалы.
Срабатываемые покрытия наносятся методами газопламенного, сверхзвукового газопламенного (СГН) или плазменного напыления. В двух последних случаях в композиции материалов вносятся специальные добавки, обеспечивающие необходимую пористость покрытий.
Жаростойкие покрытия.Основной причиной разрушения деталей горячего тракта двигателя является высокотемпературное окисление, которое может усугубляться параллельным протеканием других химических реакций (с серой, солями щелочных металлов, легкоплавкими оксидами и проч.). Свойство материалов сопротивляться высокотемпературному окислению называют жаростойкостью. Высокотемпературное воздействие кислорода на поверхности деталей может приводить к разрушению материала вследствие образования и отслаивания окисных пленок, к внутреннему окислению, возникающему в результате диффузии кислорода по границам зерен, а также к образованию твердых растворов и соединений кислорода с компонентами сплавов. В итоге снижается прочность и уровень механических свойств материала, в частности пластичность. Окисление, диффузионные процессы и механические нагрузки приводят к образованию в поверхностном слое микротрещин, пор, зон с различной твердостью и прочностью и других концентраторов напряжений.
Очевидно, что сопротивление высокотемпературному окислению определяется химической активностью металла или сплава по отношению к кислороду и свойствами образующихся окисных пленок.
Следующие факторы обусловливают защитную способность окисных пленок.
Сплошность. Сплошные пленки возникают в тех случаях, когда объем образовавшегося окисла больше объема окисленного металла.
Пористость. На многих металлах (Fe, Ti, Zr, Nb, Ta, Hf, W, Mo и др.) образуются пористые проницаемые окисные пленки, не обеспечивающие необходимую защиту от высокотемпературного окисления.
Различие в коэффициентах термического расширения окисла и основного металла, вследствие чего при колебаниях температуры, характерных для условий работы ГТД, происходит растрескивание и отслоение окисных пленок.
Различие в значениях модуля упругости окисла и основного металла.
Толщина окисной пленки. Толстые окисные пленки, образующиеся в условиях высокотемпературного окисления, являются более пористыми, чем тонкие, и имеют повышенную концентрацию дефектов.
Физико-химические свойства. Некоторые окислы при высоких и повышенных температурах становятся летучими (CrO3, MoO3), расплавляются (V2O3) или подвергаются дальнейшему окислению (Cr2O3®CrO3).
Из всего многообразия оксидов металлов наиболее стойкими являются Al2O3, Cr2O3, SiO2. По этой причине Al, Cr и Si служат базовыми элементами, используемыми в жаростойких покрытиях.
Актуальной является проблема защиты от высокотемпературной коррозии никелевых сплавов, из которых в основном изготавливаются детали горячего тракта ГТД.
В настоящее время для этих целей широко используются покрытия системы Me (Ni, Co) – Cr – Al –Y, Al – Si – Ni – Y (рис.5.6).
При выборе состава покрытия и содержания базовых элементов руководствуются следующими факторами:
- минимальным различием коэффициентов термического расширения покрытия и защищаемого сплава;
- уровнем рабочих температур и составом окислительной среды, определяющих условия формирования защитных пленок, интенсивность диффузионных процессов и скорость деградации защитных свойств покрытия;
- степенью влияния покрытия на усталостную прочность деталей;
- способом нанесения покрытия и возможностями дальнейшей обработки с целью повышения прочности сцепления, плотности, шероховатости и т.д.
Основой большинства покрытий, применяемых для защиты лопаток газовых турбин, является жаростойкая фаза b- NiAl. Для повышения ее стабильности в состав покрытия дополнительно вводятся легирующие элементы (Ta, Hf, Y, Si и др.). Введение иттрия позволяет устранить порообразование в покрытии в процессе эксплуатации и увеличивает адгезию верхней окисной пленки. Некоторые добавки увеличивают пластичность покрытия, что является важным условием его работоспособности.
|
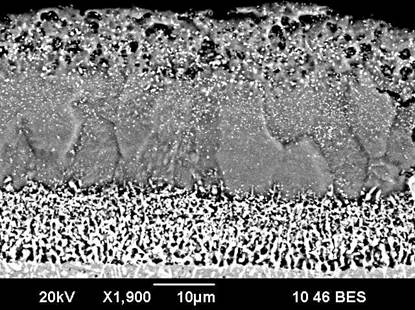
|
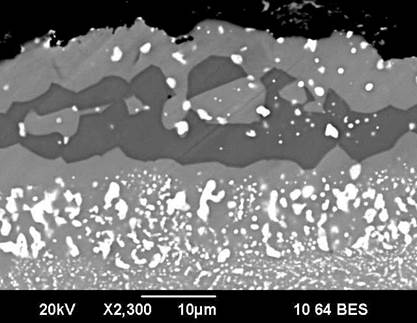
Рис. 5.6. Комбинированное жаростойкое покрытие на лопатках турбины (первоначальное нанесение покрытия Al – Si – Ni – Y дуговым вакуумным испарением на установке МАП-1 с последующим диффузионным отжигом:
а – микроструктура нового покрытия; б - после 500 часов при температуре 1000о
Деградация покрытия (рис. 5.7) происходит в результате развития диффузионных процессов, приводящих к окислению b-NiAl с ростомокисной пленки и постепенному выгоранию из материала покрытия жаростойких компонентов, что ухудшает условия залечивания разрушения защитного слоя. Следует отметить, что указанное обеднение материала может быть вызвано диффузионным рассасыванием жаростойких компонентов в подложку. В качестве диффузионных барьеров, препятствующих такому рассасыванию, используются слои из тугоплавких металлов (W, Та, Nb), обладающих малой диффузионной подвижностью, и благородные металлы (Pt, Pd, Ir).
Рис. 5.7. Развитие повреждения жаростойкого покрытия (схема):
а – исходное покрытие; б – покрытие после наработки
Жаростойкие покрытия можно получать следующими способами:
- диффузионным насыщением (порошковым и шликерным алитированием и алюмосилицированием, хромоалитированием, хромированием и силицированием);
- способами PVD (дуговое, магнетронное и электронно-лучевое испарение с последующей конденсацией);
- плазменным и сверхзвуковым газопламенным напылением и др.
Некоторые покрытия одновременно выполняют функции жаростойких и уплотнительных.
Для защиты литых лопаток турбины из сплава ЖС6У с равноосной структурой широко используется покрытие СДП-2 (Ni - 20 % Сг -12 % А1 - 0,5 % Y), наносимое дуговым вакуумным испарением на установках МАП-1. Для лопаток из сплавов ЖС26ВИ и ЖС32ВИ с монокристальной структурой используют алюминидное покрытие ВСДП-11 (AL - Si - Ni - Y), обладающее высокими защитными свойствами при температурах 1050 ... 1100 °С. Покрытие с кремнием формируется в процессе диффузионного отжига нанесенного на установке МАП-1 слоя и состоит из внешней зоны (b-NiAl) и диффузионной зоны ((b-NiAl, g’ –Ni3Al, карбиды) на границе с подложкой.
Термобарьерные покрытия. Никелевые сплавы, из которых изготавливают детали газовых турбин, имеют температуру плавления 1200 ... .1315 °С, в то время как температура газового потока составляет -1350 °С и выше. Для обеспечения работоспособности деталей в таких условиях часть воздуха, поступающего от компрессора, идет на охлаждение, что снижает эффективность двигателя и увеличивает расход топлива. Для того чтобы снизить эти потери, на детали и узлы ГТД наносят термобарьерные покрытия (ТБП).
Это позволяет улучшить качественные характеристики двигателей, уменьшить расход воздуха на охлаждение, сэкономить топливо, на 100 ... 150 °С увеличить температуру газового потока. Одновременно повышается ресурс и надежность деталей, работающих при высоких температурах, снижается выброс вредных веществ, что обусловлено более полным сгоранием горючего. ТБП одновременно защищают материал от окисления и воздействия высоких температур.
Наиболее часто в качестве материала термобарьерных покрытий используется окись циркония. Это вызвано в первую очередь ее низкой теплопроводностью, а также тем, что она имеет близкий к никелевым сплавам коэффициент термического расширения.
Для первых ТБП, наносимых на внутреннюю поверхность камеры сгорания, использовались покрытия, в которых прочная кубическая кристаллическая структура окиси циркония стабилизировалась добавками 22 % MgO. Эти покрытия работали при температурах -980 °С. При более высоких температурах происходила дестабилизация структуры ZrO2 и как следствие разрушение покрытия.
Вторым поколением ТБП стали покрытия из ZrO2, частично стабилизированные 7 % Y2O3. Они широко используются в настоящее время. Рабочие температуры таких покрытий составляют ~1090 °С. ТБП обычно состоят из двух слоев, выполняющих различные функции (рис. 5.8). Верхний керамический слой воспринимает тепловое и эрозионное воздействие газового потока и, обладая низкой теплопроводностью, снижает температуру защищаемой детали (лопатки, рубашки камеры сгорания и др.). Под керамическим слоем находится жаростойкий слой (алюмоплатиновый, NiCoCrAlY и др.), защищающий базовый металл от окисления и способствующий повышению прочности сцепления керамического слоя с подложкой. Слой окиси циркония имеет толщину ~ 250 мкм, а слой жаростойкого покрытия NiCoCrAl – толщину ~80 ... 120 мкм. В процессе эксплуатации разрушение ТБП происходит вследствие эрозии, вызванной воздействием газового потока, ослабления прочности сцепления керамического слоя покрытия с подложкой. Последнее связано с тем, что в результате диффузионных процессов на границе керамического и жаростойкого слоев образуются и растут зерна А12О3. Замедление развития таких образований является одной из важных проблем, разрешить которую можно, в частности, добавляя иттрий.
Снизить теплопроводность покрытий на основе ZrO2 удается также их многослойным нанесением (рис. 5.8). Каждый такой слой имеет столбчатую структуру. В настоящее время разрабатываются ТБП нового поколения, в том числе на основе фосфата лантана и гексоалюмината лантана. Эти материалы могут эксплуатироваться при температурах 1100 ... 1600 °С.
Для нанесения ТБП используются три основных способа: физическое осаждение испаренного электронным лучом в вакууме материала (EB-PVD), химическое осаждение паров материала (CVD) и газотермическое напыление. Каждая из этих технологий имеет свои достоинства и недостатки. Преимуществом плазменного напыления является возможность нанесения покрытия на труднодоступных поверхностях (например, внутри камеры сгорания), простота регулирования состава покрытия, низкая стоимость и высокая производительность. Для увеличения прочности сцепления покрытия с основой и повышения жаростойкости ТБП может наноситься в несколько слоев, как это показано на рис. 5.8.
|
|
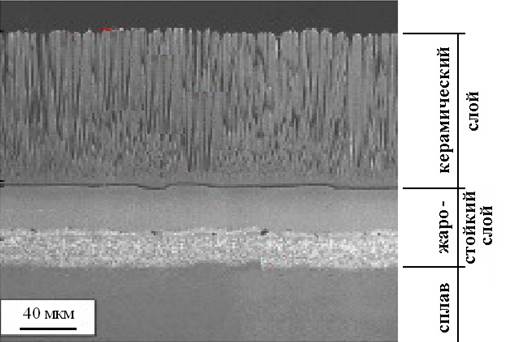
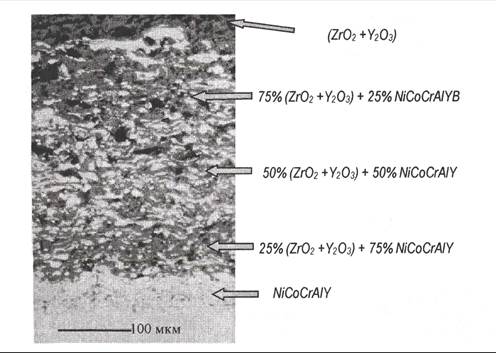
Рис. 5.8. Микроструктура термобарьерных покрытий:
а – сочетание двух слоев – керамического и жаростойкого, комбинированная технология нанесения покрытий; б – многослойное покрытие с различным содержанием керамики и жаростойкого сплава; получено плазменным напылением
ТБП первого поколения наносились плазменным напылением, а для покрытий второго поколения для наиболее ответственных деталей используют испарение керамики электронным лучом. Такие покрытия обладают повышенным сопротивлением термической усталости, имеют низкую шероховатость и высокую эрозионную стойкость. Процесс EB-PVD позволяет избежать заращивания охлаждающих отверстий в процессе нанесения покрытия. Структуры ТБП показаны на рис. 5.9.
В процессе нанесения покрытия поверхность стержня из циркониевой керамики нагревается электронным пучком в камере с высоким вакуумом. При температуре 3000°С материал стержня испаряется и образующиеся пары, конденсируясь на поверхностях деталей, формируют покрытие. Равномерность нанесения покрытия обеспечивается перемещением детали в облаке испаренного материала.
![]() |
Рис. 5.9. Структура ТБП из стабилизированного иттрием оксида циркония, нанесенного плазменным напылением (а) и методом EB-PVD (б)
на алюмоплатиновое жаростойкое покрытие
Покрытие формируется в результате осаждения отдельных атомов и молекул с образованием микроскопических столбчатых структур (столбики кристаллитов, направленных перпендикулярно поверхности). ТБП с открытой столбчатой структурой, которая считается наилучшей для термобарьерных покрытий, имеют высокие механические свойства, могут длительное время сопротивляться термическим ударам, например возникающим при работе в газовых турбинах при каждом старте и остановке, и выдерживать «забросы» температуры. Метод EB-PVD обеспечивает наибольшую прочность сцепления керамического покрытия, что обусловлено химическим взаимодействием паров керамики с металлом поверхности. ТБП, нанесенное на лопатку газовой турбины способом EB-PVD, показано на рис. 5.10.
Дополнительная информация о видах покрытий и методах их нанесения приведена в приложении 10.
![]() |
Рис. 5.10. Лопатка турбины с термобарьерным покрытием