Буровое оборудование и инструмент
Все буровые установки имеют однотипное, но разное по своим характеристикам буровое и энергетическое оборудование.
Буровое оборудование (механизмы) подразделяется на:
оборудование для спуска и подъема бурильной колонны (подъемное оборудование),состоящее из:
· вышки,
· буровой лебедки,
· талевой (полиспастовой) системы: кронблока,
талевого блока,
талевого каната,
крюка,
штропов;
оборудование для бурения скважин, состоящее из:
· ротора,
· вертлюга с буровым шлангом,
· буровых насосов,
· силового привода,
· (забойного двигателя).
Буровая вышкапредназначена для подъема и спуска бурильной колонны, установки обсадных труб в скважину, удержания бурильной колонны на весу во время бурения, а также для размещения в ней талевой системы, бурильных труб (свечей) и другого оборудования. Применяются металлические вышки башенного и мачтового (в основном А-образного) типов.
Вышки различны по грузоподъемности и высоте. Практикой установлено, что целесообразно применять вышки высотой до 28 м при бурении скважин до глубины 1200–1300 м; 41–42 м – глубиной 1300–3500 м; 53 м и более – глубиной свыше 3500 м.
Буровая лебедкапредназначена для подъема и спуска бурильной колонны в скважину, удержания ее на весу или медленного опускания (подачи) в процессе бурения, свинчивания и развинчивания труб, спуска обсадных колонн и других вспомогательных работ. Лебедка имеет четыре скорости подъема, состоит из рамы, коробки передач и трех валов. Барабан лебедки имеет тормоз с пневматическим и ручным управлением.
Талевая (полиспастовая) система буровых установок предназначена для преобразования вращательного движения барабана лебедки в поступательное (вертикальное) перемещение крюка и уменьшения нагрузки на ветви каната.
Талевая система состоит из кронблока, устанавливаемого на верхней раме вышки, стального талевого каната и подвижного талевого блока с подъемным крюком. В зависимости от условий работы и типа установки применяют талевую оснастку 3×4, или 4×5, или 5×6, или 6×7 (талевый блок имеет на один ролик меньше, чем кронблок).
Кронблок (неподвижный блок полиспаста) – неподвижная часть талевой системы – представляет собой раму, на которой смонтированы оси и опоры со шкивами: на оси кронблока посажены 5 канатных роликов. Иногда рама выполняется за одно целое с верхней частью вышки.
Талевый блок представляет собой сварной корпус (щеки). В щеках неподвижно закреплена ось, на которой, как и в кронблоке, установлены на роликовых подшипниках четыре канатных ролика.
Если кронблок имеет пять, а талевый блок четыре канатных ролика, буровая установка позволяет производить оснастку талевой системы 4×5 (возможны и другие схемы оснастки). Это значит, что талевый канат, один конец которого укреплен на барабане лебедки, а другой (мертвый) укреплен под полом буровой, будет проходить через четыре ролика талевого блока и пять роликов кронблока.
Следовательно, вес поднимаемого полиспастной системой груза распределяется на восемь струн каната. При этом получается выигрыш в силе в 8 раз, но проигрыш в 8 раз в скорости подъема груза.
Талевые канаты состоят из шести прядей проволок из высококачественной стали диаметром 1,0–2,4 мм и металлического или пенькового сердечника, пропитанного смазкой. Проволочки свиты в пряди по спиралям. Если направление прядей в канате совпадает с направлением проволочек в пряди, свивка каната называется прямой. В канатах крестовой свивки эти направления перекрещиваются. В бурении обычно применяют канаты крестовой свивки. Диаметры канатов в зависимости от грузоподъемности установки выбирают в пределах 25–38 мм (разрывное усилие соответственно 40 000–50 000 кгс). При этом запас прочности должен быть в пределах 2,7–4,0.
Буровые крюки (крюкоблоки) изготовляют в виде отдельных крюков или крюков, соединенных с талевым блоком (крюкоблоки) Крюк посредством серьги соединяется с талевым блоком и предназначен он для подвешивания бурильных труб при помощи элеватора в процессе их спуска и подъема и для подвешивания бурильных труб при помощи вертлюга во время бурения.
Штропы являются промежуточным звеном между крюком и элеватором, на котором подвешивается колонна бурильных или обсадных труб. По конструкции штропы бывают двух типов: одно- и двухветвевые. Штропы изготавливают цельнокатанными, цельнокованными, а иногда сварными, нормальной и укороченной длины.
Ротор служит для передачи вращения колонне бурильных труб, для поддержания на весу бурильной колонны во время спуско-подъемных работ и поддержания на весу обсадной колонны при спуске ее в скважину. При турбинном бурении и бурении с электробуром ротор воспринимает реактивный момент, возникающий при работе двигателя в скважине, а также используется для периодического проворачивания бурильной колонны при спуско-подъемных операциях.
Ротор состоит из трех основных узлов: станины, вращающегося стола ротора и приводного вала. Ротор имеет неподвижный корпус, в котором на подшипниках установлен стол ротора. Стол вращается карданным валом через коническую передачу, помещенную в корпусе. Стол ротора, а следовательно, и ведущая труба обычно имеет две скорости вращения. Ведущая труба укрепляется в столе при помощи вкладышей. Ротор снабжен пневматическим клиновым захватом для осуществления спуско-подъемных работ.
Вертлюг применяют для соединения талевой системы с бурильной колонной. Вертлюгвоспринимает вес колонны бурильных труб без ограничения ее вращательного движения и обеспечивает подачу промывочной жидкости во вращающиеся бурильные трубы.
Все вертлюги имеют принципиально общую конструкцию. Вертлюг состоит из двух узлов – системы вращающихся и неподвижных деталей. Неподвижную часть вертлюга подвешивают к подъемному крюку, а к вращающейся части подвешивают бурильную колонну.
Вертлюги изготавливаются грузоподъемностью 50, 75, 130, 160 и 300 т; диаметр проходного отверстия в стволе вертлюга в разных конструкциях изменяется от 75 до 100 мм.
Буровые насосы предназначены для подачи под давлением промывочной жидкости в скважину.
Обвязка буровых насосов и оборудование напорной линии. От буровых насосов промывочная жидкость по нагнетательной линии (манифольду) подается в гибкий резиновый буровой шланг и далее в вертлюг. В состав нагнетательной линии входят: компенсаторы, нагнетательный трубопровод, стояк и задвижки.
Буровые насосы для глубокого бурения должны обладать большой производительностью и развивать высокое давление. Эти требования приобретают особую важность при турбинном бурении, где насосы, помимо промывки скважины, обеспечивают еще и привод забойного двигателя.
В глубоком бурении широкое распространение получили поршневые двухцилиндровые насосы двойного действия, обеспечивающие заданную производительность независимо от изменения гидравлических сопротивлений. Для изменения производительности насосов используют сменные цилиндровые втулки и поршни различных диаметров. В связи со значительной неравномерностью подачи жидкости и сильными колебаниями давления, характерными для поршневых насосов, в бурении используют воздушные компенсаторы давления, которые устанавливаются на нагнетательной и всасывающей линиях обвязки насосов.
В настоящее время для этой цели применяют пневматические компенсаторы, в которых воздушная или газовая подушка отделяется от жидкости резиновой мембраной, что предотвращает растворение воздуха или газа в жидкости при повышении давления.
На буровой установке монтируют обычно два, а иногда три насоса, объединенные в одну систему с помощью обвязки. Промывочная жидкость от буровых насосов подается по нагнетательному трубопроводу диаметром 140, 146 мм к стояку, вертикально установленному в вышке вблизи устья скважины. Стояк высотой 10–12 м обычно также изготавливается из труб диаметром 140, 168 мм и служит для соединения нагнетательного трубопровода с буровым шлангом. Нагнетательный трубопровод, а также выкидные линии оборудуют задвижками высокого давления. Весьма полезно включение в схему обвязки подпорных центробежных насосов, подающих промывочную жидкость во всасывающую линию буровых насосов. Это повышает коэффициент наполнения камер буровых насосов, увеличивает срок службы деталей гидравлической и основных деталей приводной их части и, как показала практика, позволяет увеличить гидравлическую мощность бурового насоса.
От стояка промывочная жидкость подается в вертлюг с помощью гибкого бурового шланга.
Буровой шланг состоит из внутреннего рукава из нефтестойкой резины, оплетенного несколькими слоями прочной прорезиненной ткани, которые чередуются со стальными лентами, намотанными сплошными перекрывающимися слоями под углом 55°. Шланги имеют встроенные металлические штуцеры для соединения с вертлюгом и стояком. Внутренний диаметр шлангов изменяется от 40 до 100 мм. Шланги рассчитаны на давление 150—300 кгс/см2.
Привод буровых установок. Буровые установки имеют главный привод для лебедки, насоса и ротора, и дополнительный – для привода вспомогательных механизмов. Для главного привода наиболее широко применяют дизельные двигатели на жидком и газообразном топливе. Дизельный привод обладает жесткой характеристикой, поэтому в современных буровых установках стремятся использовать гидродинамические передачи (турботрансформаторы).
Для привода установок эксплуатационного и глубокого разведочного бурения применяют быстроходные транспортные дизели типов В2-300А(1Д-12Б), В2-400А, В2-450 и М-601. Обычно дизель устанавливается на одной раме с трансмиссией турботрансформатора или коробкой передач, образуя силовой агрегат. Трансмиссии оборудуются редуктором, одним или двумя клиноременными шкивами, шинно-пневматическими муфтами, а иногда и реверсивным устройством. С помощью трансмиссий и клиноременных передач несколько силовых агрегатов могут компоноваться в единый групповой привод, суммирующий мощность двух, трех или пяти дизелей.
В практике глубокого бурения широкое распространение получил также электропривод от промышленных сетей переменного тока, отличающийся простотой в монтаже и эксплуатации, высокой надежностью и экономичностью. На некоторых буровых установках применяют также дизель-электрический привод на переменном и постоянном токе. Возможно также оснащение буровой установки газотурбинным приводом, работающим на низкосортном топливе или попутном газе, позволяющим значительно уменьшить вес силовой установки и упростить ее эксплуатацию.
Буровые долота
Существует большое количество различных типов долот, выбор которых при бурении скважины определяется применяемым способом бурения и физико-механическими свойствами проходимых пород.
По характеру разрушения породы все буровые долота могут быть классифицированы следующим образом.
1. Долота режущего и скалывающего типа. К этой группе относятся лопастные долота, рабочая поверхность которых имеет вид плоских лопастей. Они применяются для бурения в мягких породах.
2. Долота скалывающего и дробящего типа объединяют группу шарошечных долот с полуконическими шарошками. Эти долота предназначены для бурения пород средней твердости, а также твердых пород.
3. Долота дробящего типа. К ним относятся шарошечные долота с коническими шарошками. Эти долота используются при бурении твердых пород с пропластками крепких пород.
4. Долота истирающего типа. К этой группе относятся алмазные долота, предназначенные для бурения самых крепких и абразивных пород.
По назначению все буровые долота классифицируются на две группы:
· долота, разрушающие горную породу сплошным забоем;
· долота, разрушающие горную породу кольцевым забоем (колонковые долота).
Как для сплошного, так и для колонкового бурения созданы долота, позволяющие разрушать горную породу по любому из перечисленных четырех принципов. Это облегчает подбор типа долота в соответствии с физико-механическими свойствами данной горной породы.
3.4.1. Долота для сплошного
бурения
Лопастные долота
Изготавливаются лопастные долота двух типов: двухлопастные долота РХ («рыбий хвост») (рис. 3.1) и трехлопастные долота.
Долота РХ (рис. 3.1) применяются для бурения скважин в мягких породах (реже в породах средней твердости) преимущественно роторным способом. Верхняя часть долота имеет коническую резьбу для присоединения к бурильной колонне, нижняя часть – две лопасти.
В зависимости от расположения промывочных отверстий долота РХ разделяются на два типа:
1) с верхней промывкой (рис. 3.2, б),
у которых промывочные отверстия имеют выход в верхних частях лопастей;
2) с нижней промывкой (рис. 3.2, а),
у которых выход промывочных отверстий приближен к основаниям лопастей.
Эффективность долот РХ в значительной степени зависит от соответствия механическим и абразивным свойствам разбуриваемой породы выбранного профиля заправки лопастей долота (рис. 3.3), характеризующегося углом заострения β (между передней и задней гранями лопасти), тыловым углом γ (между задней гранью лопасти и плоскостью забоя) и углом резания α (между передней гранью и плоскостью забоя). Величина β имеет весьма существенное значение. Если угол будет большим, то лопасть получится толстой и эффективность работы долота будет снижена. Однако при малых углах заострения возможны наиболее частые поломки долота.
На эффективность работы долота существенно влияет и величина α. При бурении очень мягких пород целесообразно использовать малый угол резания. В случае же бурения мягких пород, перемежающихся породами средней твердости, угол резания следует увеличивать.
Многолетний опыт эксплуатации лопастных долот привел к созданию трех типов профилей этих долот (см. рис. 3.3).
![]() |
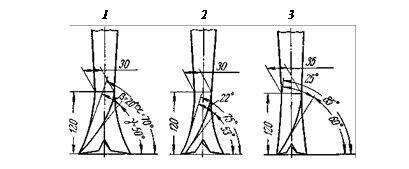
Рис. 3.3. Заправка лопастей долота:
1 – профиль № 1; 2 – профиль № 2; 3 – профиль № 3
Профиль № 1 предназначен для разбуривания вязких глин; профиль № 2 – для разбуривания песчаных и сланцевых глин, рыхлых песчаников, мягких известняков и др.; профиль № 3 – для разбуривания мергелей, сланцевых и гипсовых пропластков, меловых отложений и других не очень твердых пород.
Опыт бурения долотами РХ показал, что расположение отверстий для выхода промывочной жидкости в верхней части корпуса долота не всегда обеспечивает должную очистку забоя и хорошее охлаждение лопастей долота. Промывочная жидкость не доходит до забоя, а сразу же после выхода из отверстий поворачивает вверх и поднимается по затрубному пространству. На забое постепенно скапливается выбуренная порода, которая иногда доходит по высоте до промывочных каналов в долоте. В результате лопасти сильно нагреваются и долото быстро изнашивается.
В долотах РХ с нижней промывкой промывочные каналы подведены ближе к забою (10–15 смот забоя) и к периферии лопастей. Это обеспечивает лучшую очистку забоя, интенсивное охлаждение долота, увеличение давления струи на забой, что способствует более эффективному разрушению мягких пород.
Однако долота с нижней промывкой имеют определенные недостатки. При посадке на забой их промывочные отверстия легко забиваются, а при работе в вязких глинах на лопасти долота налипает выбуренная порода выше выхода струи жидкости из промывочных каналов. Перечисленные недостатки ограничивают применение долот РХ с нижней промывкой.
Трехлопастные долота (рис. 3.4) применяются для проходки мягких, но не вязких пород при роторном и турбинном способах бурения. Каналы для промывочной жидкости у долот этого типа подведены к каждой лопасти и находятся на расстоянии 100 ммот забоя. Основным преимуществом трехлопастных долот по сравнению с долотами РХ является более равномерное распределение осевой нагрузки, действующей на забой, что способствует более интенсивному разрушению породы.
Лопастные долота изготавливаются из высококачественной стали. Для увеличения износостойкости долота его лопасти навариваются (армируются) твердым сплавом.
Существует несколько способов армирования лопастных долот с одновременным применением твердых сплавов одного, двух или даже трех сортов. Наиболее распространенный метод армирования лопастей состоит в следующем. На лицевой поверхности лопастей заправленного по выбранному профилю долота угольным электродом выплавляются канавки, в которые в два слоя посредством вольтовой дуги наваривается зернистый твердый сплав. Кроме того, зернистый твердый сплав наваривается в один слой на всей площади лопасти долота и в три слоя – на ребрах. На зернистый твердый сплав в канавках наплавляют пластинчатый твердый сплав с соблюдением определенного порядка укладки пластин.
Шарошечные долота
Шарошечные долота успешно применяются при вращательном бурении пород самых разнообразных физико-механических свойств с промывкой забоя любой промывочной жидкостью. Созданы конструкции шарошечных долот с одной, двумя, тремя, четырьмя и даже с шестью шарошками. Наибольшее распространение получили трехшарошечные долота (рис. 3.5) диаметром от 93 до 490 мм.
Общий вид лапы шарошечного долота с подшипниками показан на рис. 3.6.
Присоедини-тельная резьба
Для эффективного бурения горных пород с различными физико-механическими свойствами изготавливаются следующие типы трех-шарошечных долот:
М – для мягких, вязких, пластичных и несцементированных пород (глины, мел, гипс);
МС – для мягких, вязких, пластичных и несцементированных пород с пропластками пластичных и хрупко-пластичных пород (глины, мел, гипс с пропластками мергеля, песчаника, сланца);
С – для пластичных и хрупко-пластичных пород средней твердости (мергели, песчаники, сланцы);
СТ – для пластичных и хрупко-пластичных пород средней твердости, переслаивающихся твердыми пропластками пород (мергели, песчаники, сланцы с пропластками загипсованного песчаника, сильно заглинизированного известняка и доломита);
Т – для хрупко-пластичных твердых и абразивных пород (песчаники, доломитизированный известняк, доломиты, ангидриты с доломитом);
ТК – для хрупко-пластичных твердых пород, перемежающихся с хрупкими твердыми и крепкими абразивными пропластками пород (песчаники, доломитизированный известняк, доломиты, ангидрит с пропластками окремнелых известняков и песчаников);
К – для хрупких крепких и абразивных пород (окремнелые известняки и песчаники).
Наибольшее распространение имеют долота, общий вид которых показан на рис. 3.7. Долота различных типов отличаются друг от друга размерами, шагом между зубьями, конструкцией зубьев, углом наклона оси шарошки к оси долота и конфигурацией шарошек.
С увеличением твердости горных пород рекомендуется применять долота с меньшей высотой зубьев и меньшим шагом между ними. Уменьшение высоты зубьев предотвращает их поломку при разбуривании твердых пород, а сокращение шага между зубьями увеличивает эффект дробления породы.
При бурении в мягких породах шлам часто налипает на шарошки, что снижает эффект работы долота и может даже привести к прихвату бурильной колонны. Поэтому зубчатые венцы на шарошках долот типа М, MС и С располагаются так, чтобы зубья одной шарошки могли очищать от налипающей породы промежутки между зубьями соседней шарошки. Такие долота называют долотами с самоочищающимися шарошками.
Как видно из рис. 3.7, зубья долота типа К отличаются по конструкции от зубьев долот других типов. Шарошки у долот типа К имеют вставные зубья из твердого сплава с полусферической рабочей поверхностью. Разрушение породы этими долотами заключается в выкалывании последней в зоне контакта зуба с плоскостью забоя. При бурении в весьма твердых породах эти долота более эффективны по сравнению с обычными трехшарошечными долотами. Это объясняется уменьшением площади контакта сферических зубьев с породой при передаче нагрузки на долото. В связи с этим удельное давление на породу увеличивается по сравнению с обычными долотами при одинаковой осевой нагрузке. Кроме того, твердосплавные вставные сферические зубья изнашиваются гораздо медленнее, чем обычные призматические зубья.
![]() |

![]() |
Одним из основных узлов шарошечного долота является опора. При современных режимах бурения опоры долота должны воспринимать при высоких скоростях вращения шарошек значительные осевые нагрузки. Однако вследствие ограниченных габаритов шарошек приходится применять довольно несовершенные подшипники.
Опоры типа I (две опоры скольжения и одна опора качения – шариковая) имеют долота малых диаметров (от 93 до 135 мм);опоры типа II (одна опора скольжения и две опоры качения – роликовая и шариковая) имеют долота средних диаметров (от 140 до 190 мм);опоры типа III (три опоры качения – роликовая, шариковая, роликовая) имеют долота больших диаметров (от 214 до 490 мм) (рис. 3.5 и 3.6).
Опоры трехшарошечных долот не имеют обойм. Для изоляции опор долота от промывочной жидкости, насыщенной абразивными частицами выбуренной породы, и обеспечения их принудительной смазки в сложных условиях, бурении на больших глубинах изготавливаются долота с герметизированными опорами.
Продолжительность работы долота на забое зависит от долговечности опоры и износостойкости зубьев шарошки. Правильно сконструированные, изготовленные и собранные опоры шарошек должны быть более долговечными, чем зубья шарошек. При этом условии обеспечивается эффективная безаварийная работа долота на забое скважины.
Размеры, форма и расположение промывочных отверстий оказывают большое влияние на эффективность работы долота. Струя промывочной жидкости очищает зубья шарошек от шлама, охлаждает рабочие элементы долота и смазывает подшипники шарошек.
Наилучшая очистка забоя от шлама в случае разбуривания твердых пород достигается при направлении струи промывочной жидкости непосредственно на забой. При бурении же в пластичных липких породах направлять струю промывочной жидкости на забой целесообразно только при большой производительности буровых насосов, при которой шарошки в достаточной степени очищаются омывающими их турбулентными потоками жидкости, отражающимися от забоя. При малой производительности буровых насосов струи жидкости, направленные на забой, не в состоянии обеспечить очистку шарошек от липкой породы. В результате уменьшается удельное давление на породу и скорость бурения резко снижается. В этих условиях наилучшие результаты получаются при направлении струй не на забой, а на шарошки.
В мягких и рыхлых породах струи жидкости, направленные на забой, не только удаляют шлам, но и разрушают породу за счет возникающего при движении жидкости гидромониторного эффекта. Опыт бурения мягких пород долотами со специальными промывочными насадками позволил создать гидромониторные долота, которые получили широкое распространение.
Тяжелые условия работы шарошечных долот обусловливают применение для их изготовления высококачественных сталей с последующей химико-термической обработкой наиболее ответственных и быстроизнашивающихся деталей (зубьев, рабочих поверхностей цапф и шарошек).
Для повышения износостойкости зубья и тыльная часть шарошек армируются зернистым твердым сплавом из литых карбидов вольфрама.
Алмазные долота
Алмазные долота применяются при проходке очень твердых пород, а также при бурении нижних интервалов глубоких скважин, где их высокая стоимость компенсируется большой долговечностью и, следовательно, снижением затрат времени на спуско-подъемные операции. В СССР выпускались алмазные долота двух типов: спиральные – для турбинного бурения (рис. 3.8, а) и радиальные – для роторного бурения (рис. 3.8, б). Высокая эффективность работы алмазного долота обеспечивается применением для их изготовления высококачественного металла и алмазов, заделанных в рабочие поверхности долота.
Опыт проходки глубоких нефтяных и газовых скважин показал, что одно алмазное долото может пройти в твердой породе до 250–300 мпри непрерывном бурении в течение 150–200 ч. Таким образом, одним алмазным долотом можно заменить более десяти шарошечных долот.
3.4.2. Долота для колонкового
бурения
В процессе бурения разведочной, а иногда и эксплуатационной скважины периодически отбираются породы в виде нетронутых целиков (кернов) для составления стратиграфического разреза, изучения литологической характеристики пройденных пород, выявления содержания нефти или газа в порах проходимых пород и т. д.
Для извлечения на поверхность керна применяются специальные долота, называемые колонковыми. При бурении керн входит внутрь такого долота и в нужный момент поднимается на поверхность.
Выпускаются колонковые долота двух типов – со съемной грунтоноской и без съемной грунтоноски. При бурении колонковыми долотами без съемной грунтоноски для подъема керна на поверхность приходится поднимать всю бурильную колонну. При работе же колонковыми долотами со съемной грунтоноской последнюю при помощи специального каната, маленькой вспомогательной лебедки и ловителя извлекают на поверхность без подъема труб.
а б
Рис. 3.8. Алмазные долота для сплошного бурения
Колонковые долота со съемной
грунтоноской
Бурение колонковыми долотами со съемной грунтоноской (керноприемником) предпочтительно при больших объемах отбора керна, что имеет место при бурении опорных, параметрических и др. скважин. Колонковые долота со съемной грунтоноской выпускаются в основном для турбинного бурения. В этом случае грунтоноска монтируется в турбобуре специальной конструкции. Поэтому описание подобного долота будет дано в разделе, посвященном турбобурам.
Колонковые долота без
съемной грунтоноски
На рис. 3.9 показано колонковое долото без съемной грунтоноски типа СДК-1 в сборе с четырехшарошечной бурильной головкой 1. Корпус долота 4 изготавливается из стандартной бурильной трубы. Внутри корпуса помещается несъемная грунтоноска 8, состоящая из кернодержателя 2, головки 6 с шариковым клапаном 5. Подшипник обеспечивает неподвижность грунтоноски во время вращения бурильной головки вместе с корпусом долота. Тип кернодержателя выбирается в зависимости от свойств проходимой породы. При бурении в мягких и сыпучих породах применяются кернодержатели, рычажки которых полностью перекрывают входное сечение керноприемной трубы (рис. 3.10, а). При бурении в породах средней твердости и в твердых устанавливаются кернодержатели, рычажки которых частично перекрывают сечение керноприемной трубы (рис. 3.10, б).
Эти долота предназначены для роторного способа бурения, но могут быть применены и при турбинном бурении.
В процессе бурения этими долотами в центре скважины образуется столбик породы – керн, который входит через кернодержатель в грунтоноску. Для подъема грунтоноски с керном требуется поднять всю бурильную колонну и долото.
Рис. 3.10. Кернодержатели
Бурильные головки для колонкового
бурения
Бурильные головки (рис. 3.11) по конструкции в основном однотипны. Состоят они из четырех соединяющихся между собой при помощи сварки лап (секций), образующих корпус головки, и шарошек, вращающихся на цапфах лап. Подшипники каждой шарошки имеют ряд роликов и два ряда шариков, из которых один ряд является одновременно замком, удер-
живающим шарошки от сползания с цапфы лапы.
Для обеспечения повышенной прочности и стойкости долот лапы, шарошки, шарики и ролики изготовляются из высоколегированных сталей и подвергаются специальной химико-термической обработке. Зубцы и тыльная часть шарошек армируются зернистым твердым сплавом. Кроме того, кернообразующие вершины шарошек укреплены запрессованными в них стержнями из твердого сплава.
Выпускаются бурильные головки диаметром от 97 до 346 ммтипов М, С, Т и К, что обеспечиваетбурение с отбором керна в скважинах разного диаметра при прохождении пород различной твердости.
Бурильная колонна
Бурильная колонна (рис. 3.12) состоит из ведущей трубы 4, бурильных труб 8 и утяжеленных бурильных труб 13. Верхняя часть бурильной колонны, представленная ведущей трубой 4, присоединяется к вертлюгу 1 при помощи верхнего переводника 3 и переводника вертлюга 2. Ведущая труба присоединяется к первой бурильной трубе 8 через нижний переводник ведущей трубы 5, предохранительный переводник 6 и муфту бурильного замка 7. Бурильные трубы 8 соединяются друг с другом при помощи бурильных замков, состоящих из двух деталей (муфты бурильного замка 7 и ниппеля бурильного замка 9), или при помощи соединительных муфт 10. Утяжеленные бурильные трубы (УБТ) непосредственно свинчиваются друг с другом без применения каких-либо соединительных элементов. Верхние УБТ присоединяются к бурильной трубе через переводник 11. К нижним УБТ 13 через переводник 14 привинчивается долото (при роторном способе бурения) или забойный двигатель с долотом (при турбинном бурении и при бурении с электробуром).
Бурильная колонна предназначена для следующих целей:
1. передачи вращения от ротора к долоту (при роторном бурении);
2. подвода промывочной жидкости: к турбобуру (при турбинном бурении), к долоту и забою скважины (при всех способах бурения);
3. монтажа отдельных секций токопровода (при бурении с электробуром);
4. создания нагрузки на долото;
5. подъема и спуска долота, турбобура,
электробура;
6. проведения вспомогательных работ
(расширение и промывка скважины,
ловильные работы, проверка глубины
скважины и т. д.).
Условия работы бурильной колонны при роторном способе и при бурении с забойными двигателями различны. При роторном способе бурильная колонна, передающая вращение от ротора к долоту и осевую нагрузку на долото, испытывает целый ряд нагрузок.
Когда бурильная колонна не касается забоя скважины и не вращается, она подвержена только растягивающим усилиям, которые достигают максимума у вертлюга. В процессе бурения скважины верхняя часть бурильной колонны растянута, а нижняя, опирающаяся на забой, – сжата.
Таким образом, бурильная колонна при бурении одновременно подвержена действию растягивающих и сжимающих усилий. При этом она всегда имеет сечение, в котором отсутствуют растягивающие и сжимающие усилия, а следовательно, и напряжения от действия этих сил.
Кроме напряжений растяжения и сжатия при передаче вращающего момента от ротора к долоту в бурильной колонне возникают напряжения кручения, которые достигают максимума у устья скважины, а также изгибающие напряжения от действия центробежных сил, увеличивающиеся от устья к забою скважины.
Одновременное действие на бурильную колонну всех перечисленных сил осложняет условия ее работы при роторном способе бурения. В результате часто случаются аварии с бурильными трубами, бурильными замками и другими элементами колонны.
При бурении скважины с забойным двигателем (турбобуром или электробуром) условия работы бурильной колонны значительно облегчаются. Она в этом случае не вращается и поэтому испытывает только растягивающие и сжимающие нагрузки, а также реактивный момент забойного двигателя. Последний имеет незначительную величину, в практических расчетах им можно пренебречь.
Таким образом, бурение с забойными двигателями в значительной степени снизило требования к бурильной колонне. Стало возможным применение для бурильной колонны труб с меньшей толщиной стенок, что сократило расход металла, а следовательно, и уменьшило ее стоимость. Число аварий с бурильной колонной при любых условиях ее работы с забойными двигателями всегда во много раз меньше, чем при роторном бурении. Рассмотрим основные элементы бурильной колонны.
Ведущая труба может иметь квадратное, шестигранное и восьмигранное сечение. На территории СНГ получили распространение ведущие трубы квадратного сечения («квадраты»). Вращающий момент от ротора передается ведущей трубе через вкладыши, вставляемые в ротор. Для каждого размера ведущей трубы применяются соответствующие вкладыши, позволяющие ей свободно перемещаться вдоль оси скважины.
Бурильные трубы выпускаются следующих конструкций:
а) с высаженными внутрь концами (рис. 3.13, а);
б) с высаженными наружу концами (рис. 3.13, б);
в) с приваренными соединительными концами.
Рис. 3.13. Бурильная труба:
а – с высаженными внутрь концами; б – с высаженными наружу концами;
I – труба; II – муфта
Бурильные трубы с высаженными внутрь концами имеют конусную мелкую трубную резьбу. Высадка внутрь на концах трубы уменьшает ее внутренний диаметр. Соединяются такие трубы при помощи замков (рис. 3.14, а) или муфт (рис. 3.14, б). Трубы данной конструкции в настоящее время весьма распространены. Выпускаются они длиной 6; 8 и 11,5 мс наружным диаметром 60, 73, 89 и 102 мм. Трубы диаметром 114, 127, 140 и 168 ммвыпускаются длиной 11,5 м.
б
Рис. 3.14. Соединение бурильных труб с высаженными внутрь концами:
а – бурильным замком; б – соединительной муфтой
Бурильные трубы с высаженными наружу концами имеют такую же резьбу, как и трубы с высаженными внутрь концами. Высадка наружу позволяет иметь одинаковый внутренний диаметр по всей длине трубы, что резко улучшает гидравлическую характеристику этих труб по сравнению с трубами с высаженными внутрь концами, так как значительно снижаются потери на преодоление сопротивлений при прохождении промывочной жидкости по бурильной колонне.
Рассматриваемые трубы соединяются также при помощи соединительных муфт или бурильными замками. Они имеют такую же длину, что и трубы с высаженными внутрь концами. Заводы выпускают трубы диаметром 60, 73, 89, 102, 114 и 140 мм.
Сначала эти трубы предназначались для бурения скважин электробуром. При этом способе бурения требуется наличие в трубах широкого и одинакового по всей длине циркуляционного канала, обеспечивающего монтаж токоподвода и прохождение промывочной жидкости. Однако опыт показал целесообразность применения этих труб при турбинном способе бурения.
В процессе спуска и подъема бурильной колонны нецелесообразно свинчивать и развинчивать все трубы, имеющиеся в колонне. Гораздо быстрее осуществляются спуско-подъемные операции при отвинчивании или навинчивании сразу нескольких труб. Комплект таких труб, называемый свечой, может иметь разную длину, зависящую от высоты применяемой вышки.